

Six Sigma tools for DMAIC Phases
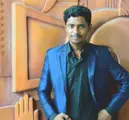
- 48 Comments
- Published on Nov 8 2024
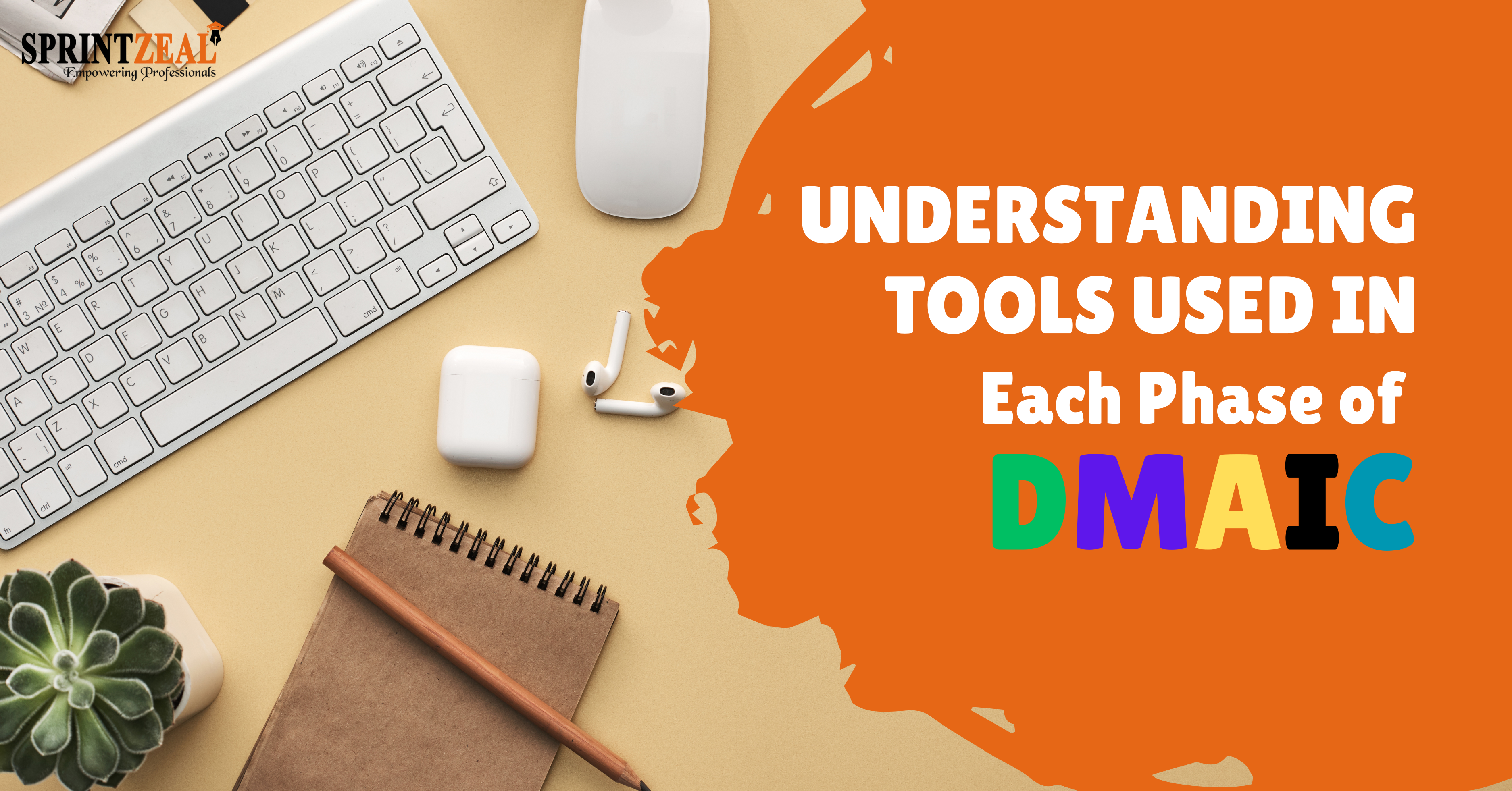
What Are DMAIC Tools?
Skip Introduction
DMAIC is an acronym for Define, Measure, Analyze, Improve, and Control. The DMAIC methodology is a systematic problem-solving methodology widely used in Lean Six Sigma projects to enhance processes and improvements. DMAIC tools help practitioners navigate each phase of this structured approach.
Defining DMAIC Tools
DMAIC tools encompass a diverse set of techniques and methodologies designed to assist in specific phases of the DMAIC process. These tools serve as valuable aids for data collection, analysis, and decision-making, ultimately contributing to the successful execution of Lean Six Sigma projects.
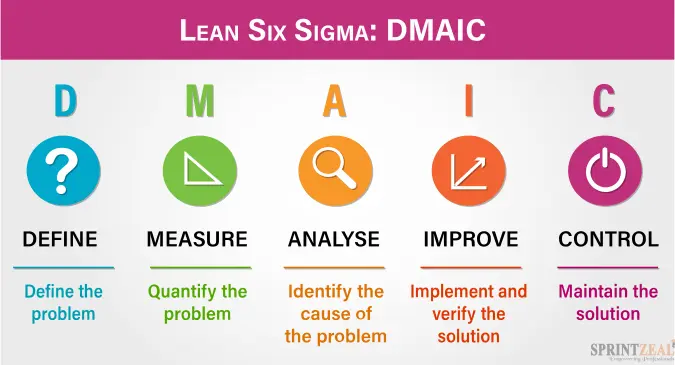
- Define phase tools help in clarifying project goals, scope, and key stakeholders.
- Measure phase tools are used to collect and analyze data to establish the current state of the process.
- Analyze phase tools identify root causes of problems and gaining insights into process behavior.
- Improve phase tools and techniques support the development and implementation of solutions.
- Control phase tools that ensure sustained improvements and maintain process stability.
Let’s dive in and understand the tools used for each of the 5 DMAIC phases and explore how they help in Lean Six Sigma projects.
Table of Contents
Top 5 tools for each of the dmaic phases, dmaic tools for define phase, dmaic tools for measure phase, dmaic tools for analyze phase, dmaic tools for improve phase, dmaic tools for control phase, selecting the right dmaic tools, faqs for dmaic tools.
Master DMAIC Tools with Lean Six Sigma Certification Training
Effective process improvement relies on choosing the right tools for each step of the DMAIC approach. Every phase demands specific tools to tackle its particular challenges. In this section, we'll explore the top five tools for each phase, explaining how they're used and why they matter for making processes better and ensuring top-notch quality in organizations.
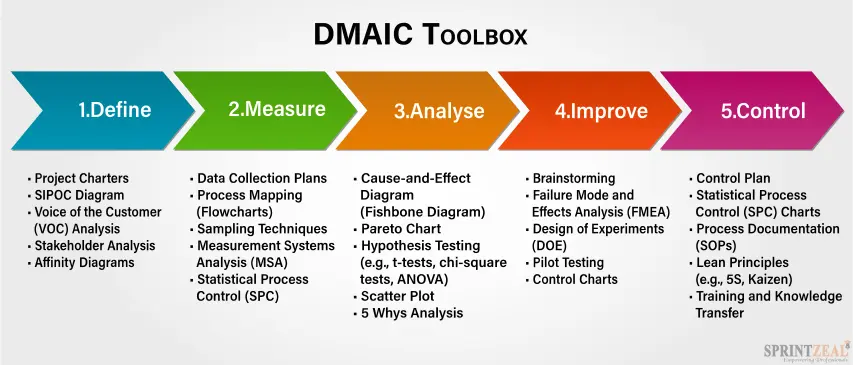
In the Define phase of the DMAIC methodology, the primary objective is to establish a clear understanding of the problem, project goals, and scope. This phase sets the stage for the entire project, and five key DMAIC tools assist in achieving these critical objectives:
1. Project Charter
What is a Project Charter? A project charter is a foundational document that outlines the purpose, scope, objectives, and key stakeholders of the project. It serves as a roadmap, providing clarity and direction from the very beginning.
How it helps:
- Establishes Purpose: The project charter defines the reason for undertaking the project, ensuring that all team members are aligned with its goals and objectives. - Defines Scope: It clearly outlines the boundaries of the project, helping the team stay focused on addressing the relevant issues. - Identifies Stakeholders: The charter lists key stakeholders, ensuring that their needs and expectations are considered throughout the project's lifecycle.
2. SIPOC Diagram
What is a SIPOC Diagram? The SIPOC (Suppliers, Inputs, Process, Outputs, Customers) diagram is a visual representation that provides an overview of the high-level process flow, including its inputs, outputs, and key stakeholders. It is instrumental in identifying areas that require improvement.
How it Helps:
- Process Clarity: SIPOC diagrams offer a clear and concise overview of the process, making it easier to identify its components and interactions. - Identifies Boundaries: By delineating the process boundaries, the SIPOC helps the team focus on specific process steps critical to the project. - Stakeholder Inclusion: It highlights the roles of customers and suppliers, ensuring that their perspectives are considered during problem-solving and decision-making.
3. Voice of the Customer (VOC) Analysis
What is VOC Analysis? Understanding the customer's needs and expectations is paramount. VOC analysis tools, such as surveys, interviews, and direct feedback collection, help gather customer insights and translate them into actionable project goals.
- Customer-Centric Approach: VOC analysis ensures that project objectives are closely aligned with what customers value most, fostering customer satisfaction and loyalty. - Data-Driven Insights: It provides invaluable data and insights directly from customers, guiding project decisions based on actual customer preferences. - Prioritization: VOC analysis helps prioritize project objectives based on the significance of specific customer needs and their potential impact on satisfaction.
4. Affinity Diagram
What is an Affinity Diagram? An affinity diagram is a tool used to organize and group large amounts of unstructured information or ideas into meaningful categories. It is particularly useful when dealing with complex or unclear problem statements.
- Idea Organization: Affinity diagrams help in structuring and categorizing ideas or data gathered during the project's initial stages. - Pattern Recognition: It allows teams to identify patterns and relationships among various pieces of information, leading to deeper insights. - Enhanced Problem Definition: Organizing information coherently, contributes to refining the problem statement and project objectives.
5. Stakeholder Analysis
What is Stakeholder Analysis? Stakeholder analysis is a systematic process of identifying and assessing the interests, influence, and potential impact of individuals or groups that have an interest in the project.
- Prioritization of Stakeholders: Stakeholder analysis helps in determining which stakeholders have the most significant influence on the project's success. - Communication Strategy: It informs the development of tailored communication plans and engagement strategies for different stakeholder groups. - Risk Mitigation: By understanding stakeholder interests and potential concerns, the team can proactively address issues that may arise during the project.
In the Define phase, these five DMAIC tools play a pivotal role in laying a solid foundation for your Lean Six Sigma project. They facilitate the process of defining the problem, project scope, and stakeholder expectations, all of which are essential for a successful project journey.
In the Measure phase of the DMAIC methodology, the primary focus is on collecting and analyzing data to establish the current state of the process. The following DMAIC tools are instrumental in achieving these objectives:
1. Data Collection Plan
What is a Data Collection Plan? A data collection plan is a structured document that outlines what data needs to be collected, how it will be collected when it will be collected, and who will be responsible for data gathering. It ensures that data is collected systematically and accurately.
- Systematic Data Gathering: Provides a clear plan for collecting relevant data points in an organized manner.
- Reduces Bias: Minimizes the risk of bias in data collection by specifying methods and procedures.
- Efficient Resource Allocation: Helps allocate resources efficiently for data collection activities.
2. Process Mapping
What is Process Mapping? Process mapping tools like flowcharts and value stream maps provide a visual representation of the process. They help in understanding the sequence of steps, inputs, and outputs in the process.
- Visual Clarity: Offers a clear visual representation of the process, making it easier to identify bottlenecks and inefficiencies.
- Identifies Handoffs: Highlights points where work is handed off between individuals or departments, which can be sources of delays.
- Root Cause Analysis: Facilitates the identification of areas within the process that may need improvement.
3. Measurement Systems Analysis (MSA)
What is Measurement Systems Analysis (MSA)? MSA tools assess the accuracy, precision, and reliability of measurement systems to ensure that collected data is trustworthy. Common MSA techniques include Gage R&R (Repeatability and Reproducibility) studies.
- Data Reliability: Ensures that measurement instruments and methods are reliable, reducing the risk of incorrect conclusions. - Identifies Measurement Error: Helps identify and quantify sources of measurement error, allowing for data correction. - Improves Decision-Making: Reliable measurements lead to better-informed decisions.
4. Histograms and Frequency Plots
What are Histograms and Frequency Plots? Histograms and frequency plots are graphical tools used to display the distribution of data. Histograms provide a visual representation of data distribution, while frequency plots show how data points are distributed across different categories or bins.
How they Help:
- Data Distribution Visualization: Provides a clear picture of how data is distributed, whether it's normally distributed or skewed. - Identifies Patterns: Helps identify patterns or outliers in the data, which may indicate process variations. - Basis for Analysis: Serves as the foundation for further statistical analysis.
5. Process Capability Analysis
What is Process Capability Analysis? Process capability analysis assesses the ability of a process to consistently produce products or services that meet customer specifications. Common metrics used in process capability analysis include Cp, Cpk, Pp, and Ppk.
- Quality Assessment: Determines whether a process is capable of producing products or services within customer-defined limits. - Focuses Improvement Efforts: Identifies areas where process capability falls short, guiding improvement efforts. Predictive Insights: Helps predict the likelihood of producing defects or non-conforming products.
The Analyze phase of the DMAIC methodology focuses on identifying the root causes of problems and gaining insights into process behavior. To achieve these objectives, various DMAIC tools are employed:
1. Cause-and-Effect Diagram (Fishbone Diagram)
What is a Cause-and-Effect Diagram? Also known as a Fishbone or Ishikawa diagram, this tool helps visualize potential causes of a problem. It resembles a fishbone, with the problem statement at the "head" and branches representing different categories of potential causes.
- Root Cause Identification: Facilitates a structured approach to identifying root causes by breaking down potential contributors. - Team Collaboration: Encourages team collaboration and brainstorming to explore various causes. - Visual Representation: Provides a clear and visual overview of the problem's causes and their relationships.
2. Pareto Chart
What is a Pareto Chart? A Pareto chart is a bar chart that prioritizes issues or causes by showing which factors contribute the most to a problem. It follows the Pareto principle, suggesting that a small number of causes (the "vital few") often account for the majority of the problems.
- Prioritization: Helps prioritize improvement efforts by focusing on the most significant contributors to the problem. - Data-Driven Decision Making: Provides a data-driven basis for determining where resources should be allocated. - Visual Clarity: Offers a clear visual representation of the most critical issues.
3. Hypothesis Testing
What is Hypothesis Testing? Hypothesis testing involves using statistical methods to analyze data and test hypotheses about potential root causes. Common tests include t-tests, chi-square tests, and ANOVA (Analysis of Variance).
- Statistical Validation: Validates whether a potential cause is statistically significant in contributing to the problem. - Data-Driven Decision Making: Provides a rigorous approach to making decisions based on data. - Evidence-Based Insights: Offers insights into which factors are likely causing the observed issues.
4. Scatter Plot
What is a Scatter Plot? A scatter plot displays data points on a two-dimensional graph, with one variable on the x-axis and another on the y-axis. It is used to explore relationships and correlations between variables.
- Visualizing Relationships: Helps visualize the relationship between two variables, indicating whether they are positively, negatively, or not correlated. - Identification of Patterns: Can reveal patterns, trends, or outliers in the data. - Data-Driven Insights: Provides a basis for making informed decisions about potential causes.
5. Five Whys Analysis
What is 5 Whys Analysis? The 5 Whys technique involves repeatedly asking "Why?" to dig deeper into the root cause of a problem. By asking "Why?" five times (or more), it aims to uncover the underlying issues.
- Systematic Inquiry: Encourages a systematic and structured approach to uncovering root causes. - Deep Understanding: Helps reach the core issues rather than addressing surface-level symptoms. - Simplicity: A straightforward yet effective technique for root cause analysis.
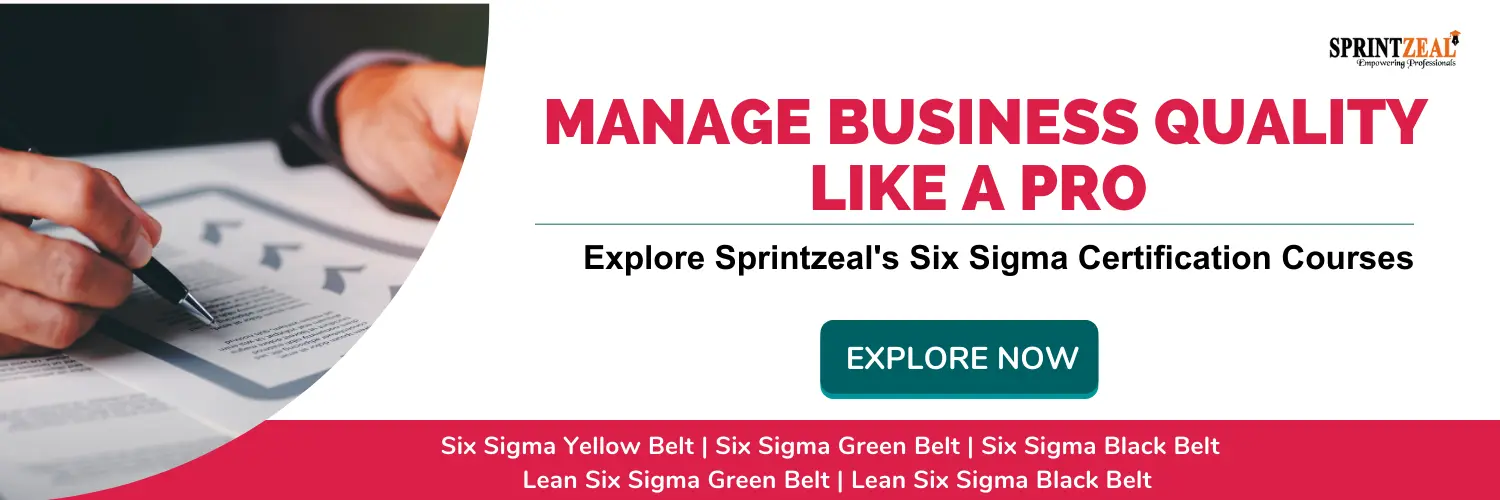
In the Improve phase of the DMAIC methodology, the focus shifts to developing and implementing solutions to address the root causes identified during the Analyze phase. The following DMAIC tools and techniques are instrumental in driving process improvement:
1. Brainstorming
What is Brainstorming? Brainstorming is a creative problem-solving technique that involves generating a wide range of ideas and potential solutions. Team members collaborate to explore innovative ways to address identified issues.
- Idea Generation: Encourages the generation of diverse ideas and solutions from team members. - Promotes Teamwork: Fosters collaboration and participation, allowing for a variety of perspectives. - Divergent Thinking: Supports thinking "outside the box" to identify novel solutions.
2. Failure Mode and Effects Analysis (FMEA)
What is FMEA? FMEA is a systematic approach to evaluating potential failure modes within a process and their potential impact. It assigns scores for Severity, Occurrence, and Detection to prioritize which failure modes to address first.
- Risk Prioritization: Identifies high-priority failure modes that pose the greatest risk to the process. - Structured Approach: Provides a structured framework for analyzing and addressing potential failures. - Focus on Prevention: Helps teams proactively address issues before they occur.
3. Design of Experiments (DOE)
What is the Design of Experiments (DOE)? DOE is a statistical technique used to systematically vary and analyze multiple factors simultaneously to optimize a process. It helps identify the ideal combination of factors that produce the desired outcomes.
- Optimization: Aids in finding the most efficient and effective combination of process variables. - Reduces Variation: Helps reduce process variability by identifying and controlling influential factors. - Data-Driven Decision Making: Provides empirical evidence for process improvements.
4. Pilot Testing
What is Pilot Testing? Pilot testing involves implementing proposed process improvements on a smaller scale before full-scale implementation. It allows for testing and refinement of solutions while minimizing risk.
- Risk Mitigation: Reduces the risk of implementing changes that may have unforeseen negative consequences. - Refinement: Provides an opportunity to fine-tune solutions based on real-world testing. - Validation: Ensures that proposed improvements work effectively in practice.
5. Control Charts
What are Control Charts? Control charts are graphical tools used to monitor and visualize process performance over time. They help identify trends, shifts, or abnormal variations in the process.
- Real-Time Monitoring: Allow for continuous monitoring of process performance. - Early Detection: Highlight deviations from the desired process state, enabling timely corrective actions. - Process Stability: Help ensure that improvements are sustained over the long term.
1. Control Charts
2. Statistical Process Control (SPC) Charts
What are SPC Charts? SPC charts, including control charts and run charts, are used to monitor process stability and identify variations. They provide a visual representation of data over time.
- Continuous Monitoring: Enable real-time monitoring of process variation and performance. - Early Detection: Alert teams to potential issues or deviations before they impact product or service quality. - Data-Driven Decision Making: Support decisions based on factual data.
3. 5S Methodology
What is the 5S Methodology? The 5S methodology focuses on organizing and maintaining a clean, efficient, and safe work environment. It comprises five principles: Sort, Set in order, Shine, Standardize, and Sustain.
- Efficiency: Reduces waste, enhances organization, and improves efficiency. - Safety: Promotes a safe and clutter-free workplace. - Sustainability: Encourages a culture of cleanliness and orderliness.
4. Poka-Yoke (Mistake-Proofing)
What is Poka-Yoke? Poka-Yoke refers to error-proofing or mistake-proofing techniques designed to prevent errors and defects during the production or operation of a process. These can include simple mechanisms or processes that prevent mistakes.
- Error Prevention: Eliminates the possibility of errors or defects at their source. - Quality Improvement: Ensures that products or services are produced correctly the first time. - Cost Reduction: Reduces the need for rework or corrections.
5. Standard Operating Procedures (SOPs)
What are Standard Operating Procedures (SOPs)? SOPs are documented step-by-step instructions that detail how specific tasks or processes should be performed. They provide a consistent and standardized approach to tasks.
- Consistency: Ensure that tasks are performed consistently and correctly. - Training: Aid in the training of new employees by providing clear instructions. - Compliance: Support compliance with regulatory requirements and quality standards.
Selecting the right DMAIC tools is crucial for the success of your Lean Six Sigma project. The choice of tools should be driven by the specific objectives of each phase and the nature of the problem you're addressing. Here's a guide to help you select the most appropriate tools for your project:
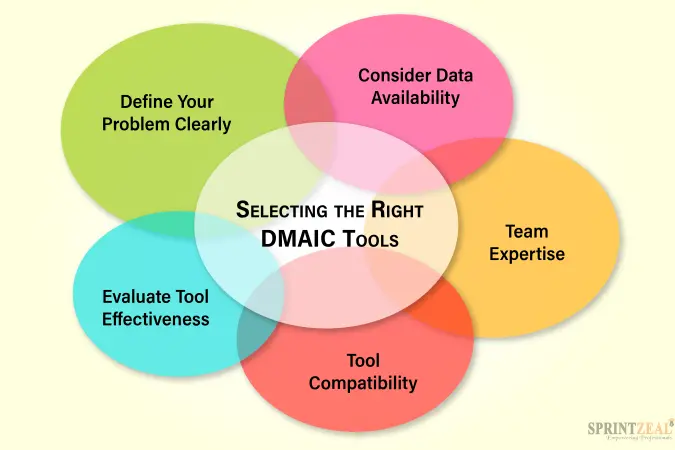
- Define Your Problem Clearly
Before choosing DMAIC tools, ensure you have a clear and concise understanding of the problem you're trying to solve. Define the problem statement, its scope, and the goals of your project. This clarity will guide your tool selection.
- Consider the DMAIC Phase
Different phases of the DMAIC process require different tools. For example:
1. In the Define phase , tools like Project Charters and SIPOC diagrams help scope and understand the problem. 2. In the Measure phase , tools like Data Collection Plans and Process Mapping are valuable for data collection and process assessment. 3. In the analysis phase , tools like Cause-and-Effect diagrams and Hypothesis Testing help identify root causes. 4. In the Improve phase , tools like Brainstorming and Design of Experiments support solution development. 5. In the Control phase , Control Charts and Standard Operating Procedures help sustain improvements.
- Consider Data Availability
The availability of data can influence your tool selection. If data is limited, focus on tools that can work with the available data or consider data collection methods for missing information.
- Team Expertise
Assess the expertise of your project team. Some tools may require specialized knowledge or training. Ensure that your team is comfortable using the selected tools or invest in training if needed.
- Tool Compatibility
Ensure that the chosen DMAIC tools are compatible with your organization's systems and processes. This includes considering software compatibility, data integration, and overall alignment with existing practices.
- Evaluate Tool Effectiveness
Regularly evaluate the effectiveness of the tools you're using. If a tool is not producing the desired results or insights, be open to adjusting your approach and considering alternative tools.
- Seek Guidance
Don't hesitate to seek guidance from experienced Lean Six Sigma practitioners, mentors, or consultants. They can provide valuable insights into which tools are best suited to your specific project and organizational context.
- Documentation
Document your tool selection process and rationale. This documentation will not only help you make informed decisions but also serve as a reference for future projects.
Remember that the effectiveness of DMAIC tools relies on their appropriate application within the context of your project. Selecting the right tools and using them effectively is a key factor in achieving successful outcomes and process improvements.
Best DMAIC Tools for the Analyze Phase?
Some of the best DMAIC tools commonly used in the Analyze phase include:
- Cause-and-Effect Diagram (Fishbone Diagram) - Pareto Chart - Hypothesis Testing - Scatter Plot - 5 Whys Analysis
What Tools Are Most Commonly Used in DMAIC?
DMAIC involves a wide range of tools, and the choice of tools depends on the specific phase of the DMAIC process and the nature of the problem being addressed. However, some commonly used tools across the DMAIC phases include:
- Define Phase: Project Charters, SIPOC diagrams. - Measure Phase: Data Collection Plans, Process Mapping. - Analyze Phase: Cause-and-Effect Diagrams, Pareto Charts, Hypothesis Testing. - Improve Phase: Brainstorming, Design of Experiments (DOE). - Control Phase: Control Charts, Standard Operating Procedures (SOPs).
What Is the Purpose of DMAIC Tools?
The purpose of DMAIC tools is to provide a structured and systematic approach to problem-solving and process improvement. These tools help organizations:
- Identify and define problems or challenges. - Measure and analyze data to understand the current state of processes. - Analyze root causes of problems. - Develop and implement effective solutions. - Maintain and control improved processes to ensure sustainability and consistency.
DMAIC tools promote data-driven decision-making and continuous improvement within an organization.
Is DMAIC a Problem-Solving Tool?
DMAIC (Define, Measure, Analyze, Improve, Control) is not a single problem-solving tool but a comprehensive problem-solving methodology used in Lean Six Sigma. It incorporates a wide range of tools and techniques at each phase to address specific aspects of process improvement and problem-solving. DMAIC provides a structured framework for identifying, analyzing, and resolving problems to enhance process performance and quality.
Improving your expertise in DMAIC tools and Lean Six Sigma methods is a valuable journey that can greatly benefit your career and your company's achievements. Lean Six Sigma Certification Training is the path to gaining this expertise in a structured and hands-on way.
Sprintzeal's Lean Six Sigma Certification Training is your gateway to achieving expertise in a structured and practical manner.
Our comprehensive training programs provide an in-depth understanding of DMAIC tools, principles, and methodologies. You'll gain hands-on experience, working on real projects that empower you to confidently apply DMAIC tools in your workplace. With a strong emphasis on problem-solving and critical-thinking skills, our training equips you to identify and address process issues efficiently.
Quality optimization and career advancement await you. Sprintzeal's Lean Six Sigma Certification opens doors to new opportunities, positioning you as a valued professional in quality management, process improvement, and leadership roles. Don't miss your chance to become a Lean Six Sigma expert—visit our Lean Six Sigma Certification Training page to embark on your DMAIC tools mastery journey with Sprintzeal today.
In this guide, we've explored DMAIC tools, pivotal in Lean Six Sigma methodology. From Define to Control, these tools empower organizations to enhance efficiency and deliver higher-quality products and services. Applying the right tool at the right time is the key to identifying root causes and achieving sustained improvements. Now, let's take your understanding of DMAIC tools further by considering Lean Six Sigma Certification Training.
In conclusion, DMAIC tools are vital for process improvement and quality optimization across diverse industries. Their universal applicability makes them a critical asset for organizations striving to reduce costs and enhance product and service delivery.
Consider taking your knowledge of DMAIC tools to the next level through Lean Six Sigma Certification Training . Sprintzeal offers comprehensive training programs designed to equip you with the expertise needed to excel in process improvement. Our experienced instructors, practical projects, and respected certifications validate your proficiency in DMAIC tools and Lean Six Sigma methodologies.
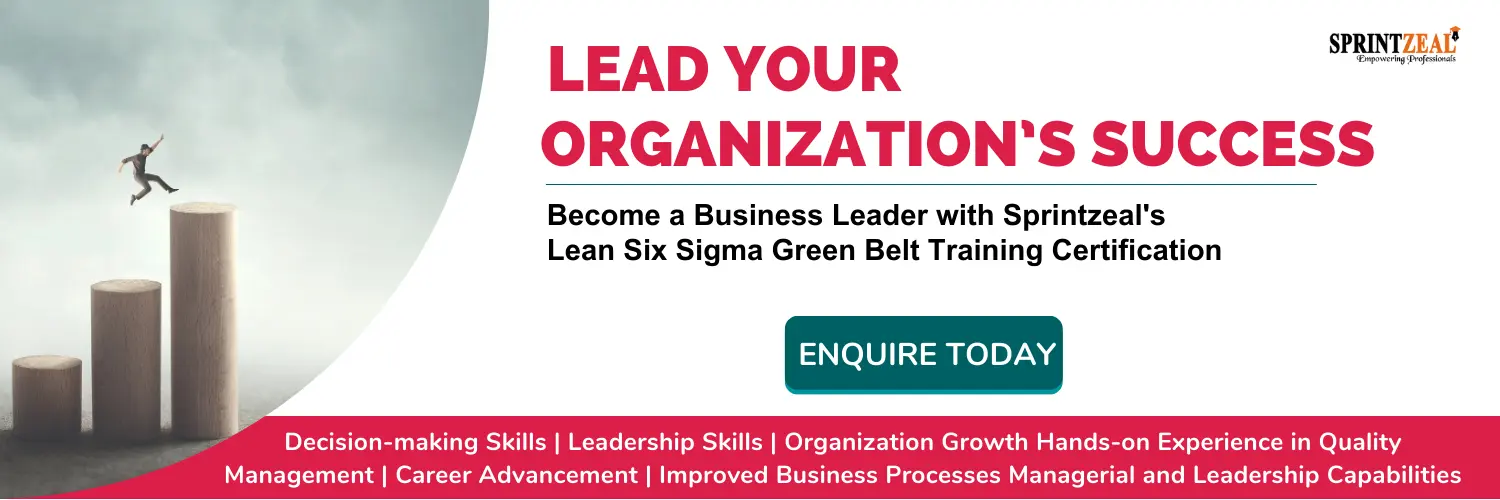
Visit our home page Sprintzeal.com to explore your options and start your path to excellence in process improvement and quality optimization. Your DMAIC tools mastery journey begins here.
Subscribe to our Newsletters
Explore program.

Apply for Free Consultation
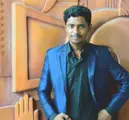
Sushmith
Our technical content writer, Sushmith, is an experienced writer, creating articles and content for websites, specializing in the areas of training programs and educational content. His writings are mainly concerned with the most major developments in specialized certification and training, e-learning, and other significant areas in the field of education.
Popular Programs
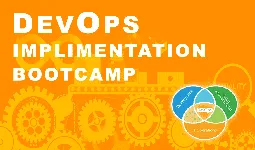
DevOps Implementation Boot Camp
Live virtual training.
- 4.6 (477 + Ratings)
- 53k + Learners
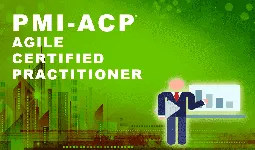
PMI - ACP® - Agile Certified Practitioner
- 4.5 (798 + Ratings)
- 71k + Learners
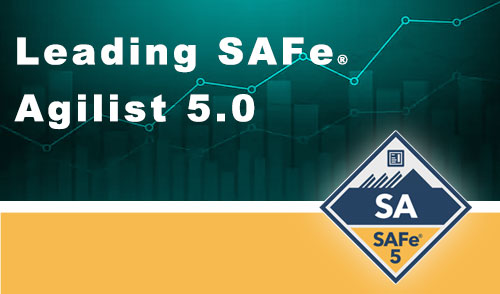
Leading SAFe® 5 Agilist
- 4.4 (64 + Ratings)
- 35k + Learners
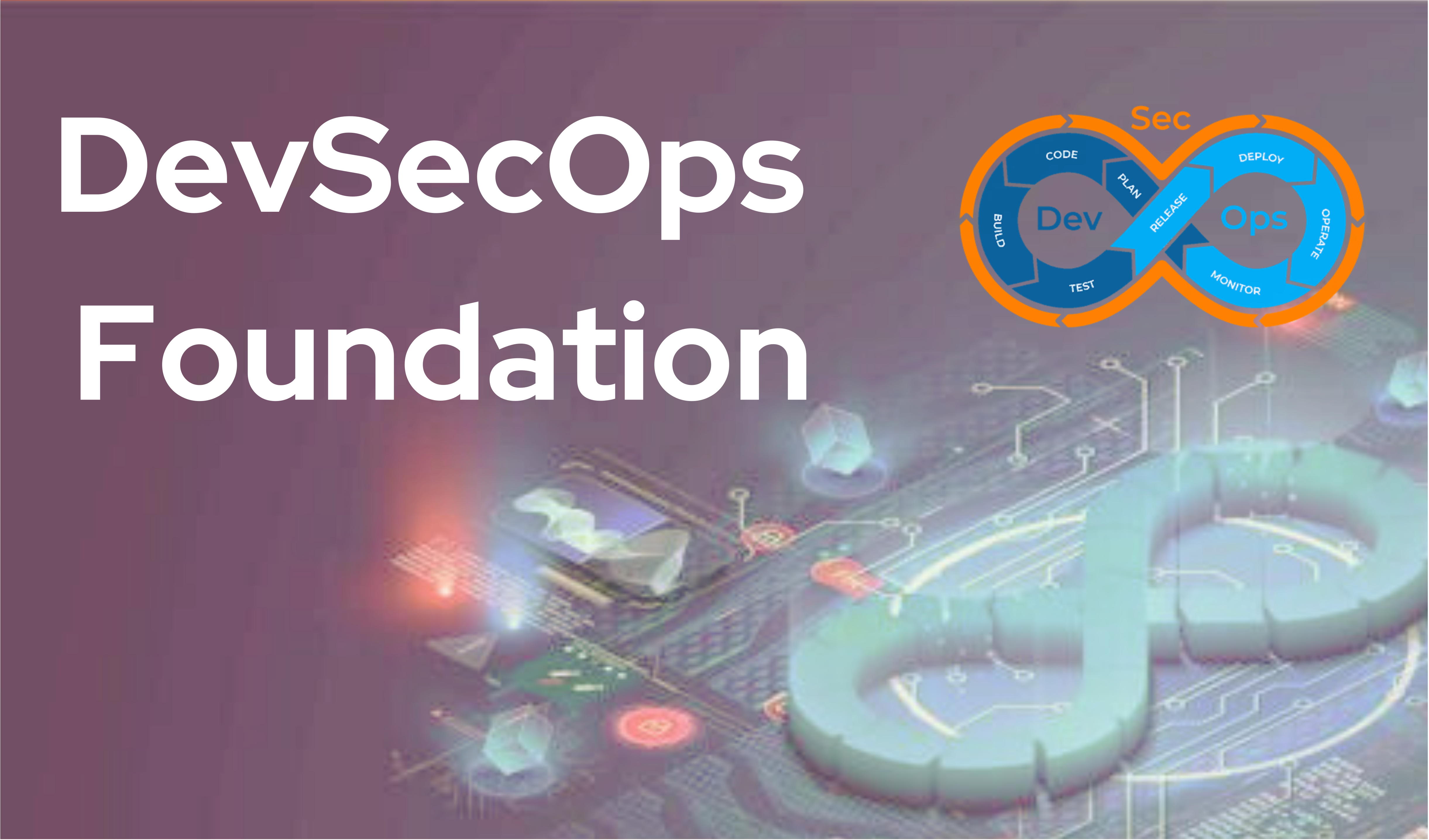
DevSecOps Foundation
- 4.6 (650 + Ratings)
- 61k + Learners
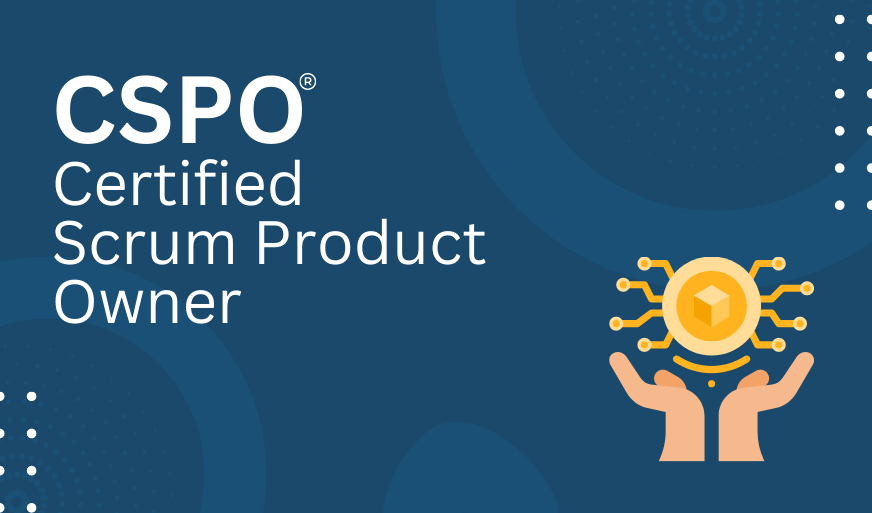
CSPO® - Certified Scrum Product Owner
- 4.5 (952 + Ratings)
- 48k + Learners
.webp)
CSM® - Certified Scrum Master
- 4.6 (952 + Ratings)
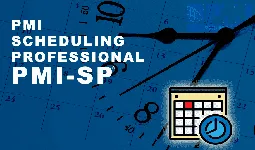
PMI-SP® - Scheduling Professional
- 4.3 (736 + Ratings)
- 13k + Learners
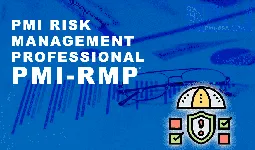
PMI-RMP® - Risk Management Professional
- 4.1 (963 + Ratings)
- 41k + Learners
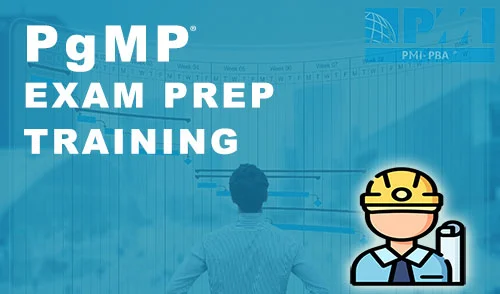
PgMP Exam Prep Training
- 5 (650 + Ratings)
- 4k + Learners
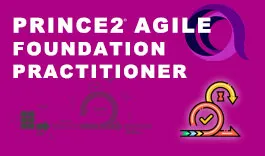
PRINCE2® Agile - Foundation Practitioner
- 4.4 (100 + Ratings)
- 24k + Learners
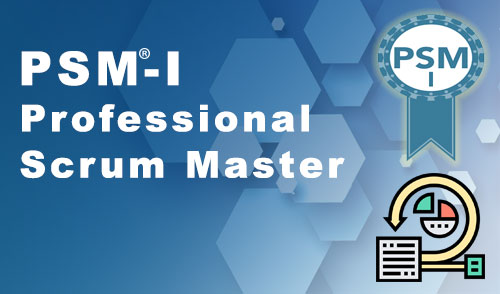
PSM® - Professional Scrum Master Certification
- 4.7 (75 + Ratings)
- 10k + Learners
Trending Posts
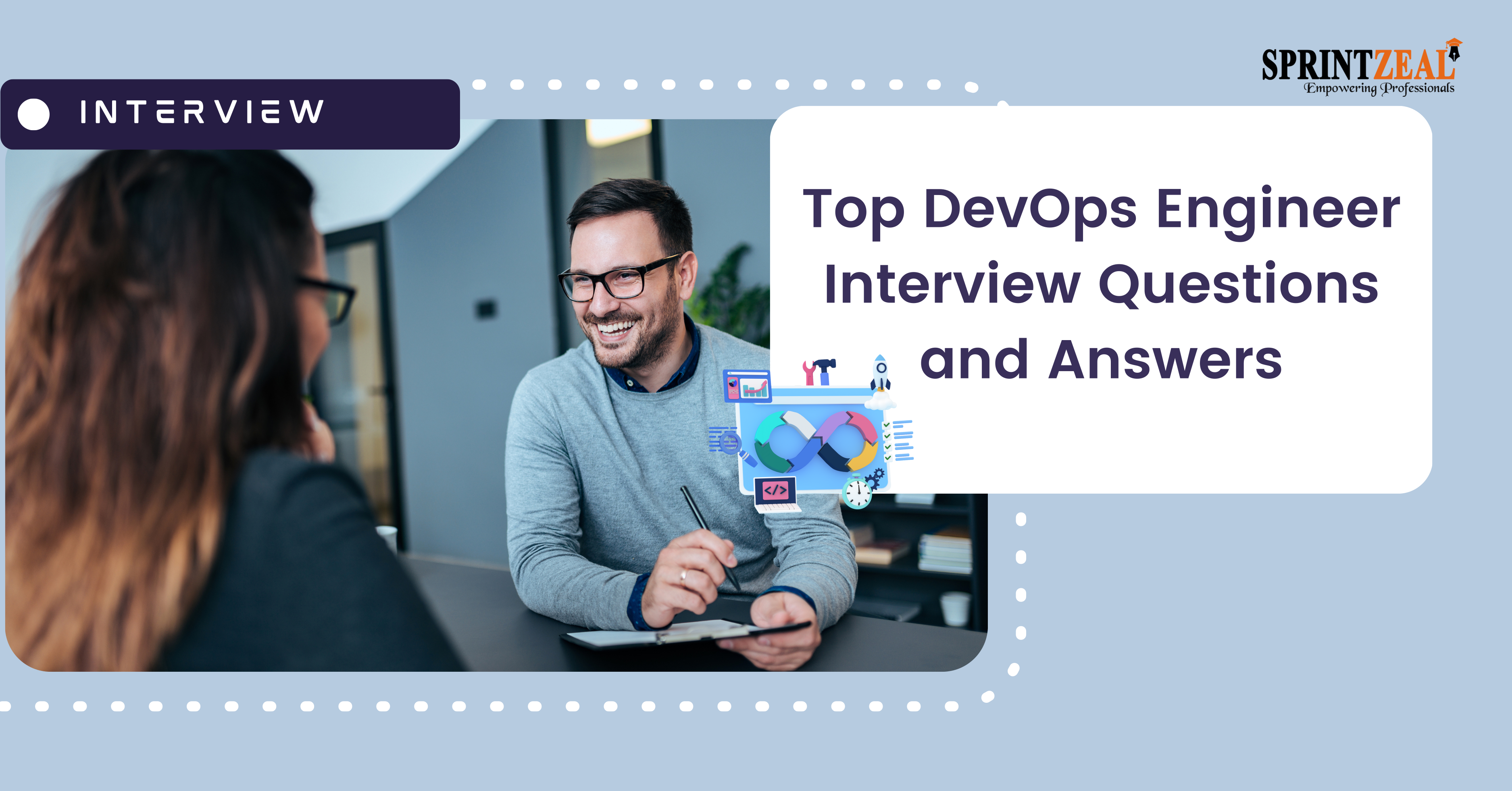
DevOps Engineer Interview Questions - Best of 2024
Last updated on Feb 6 2024
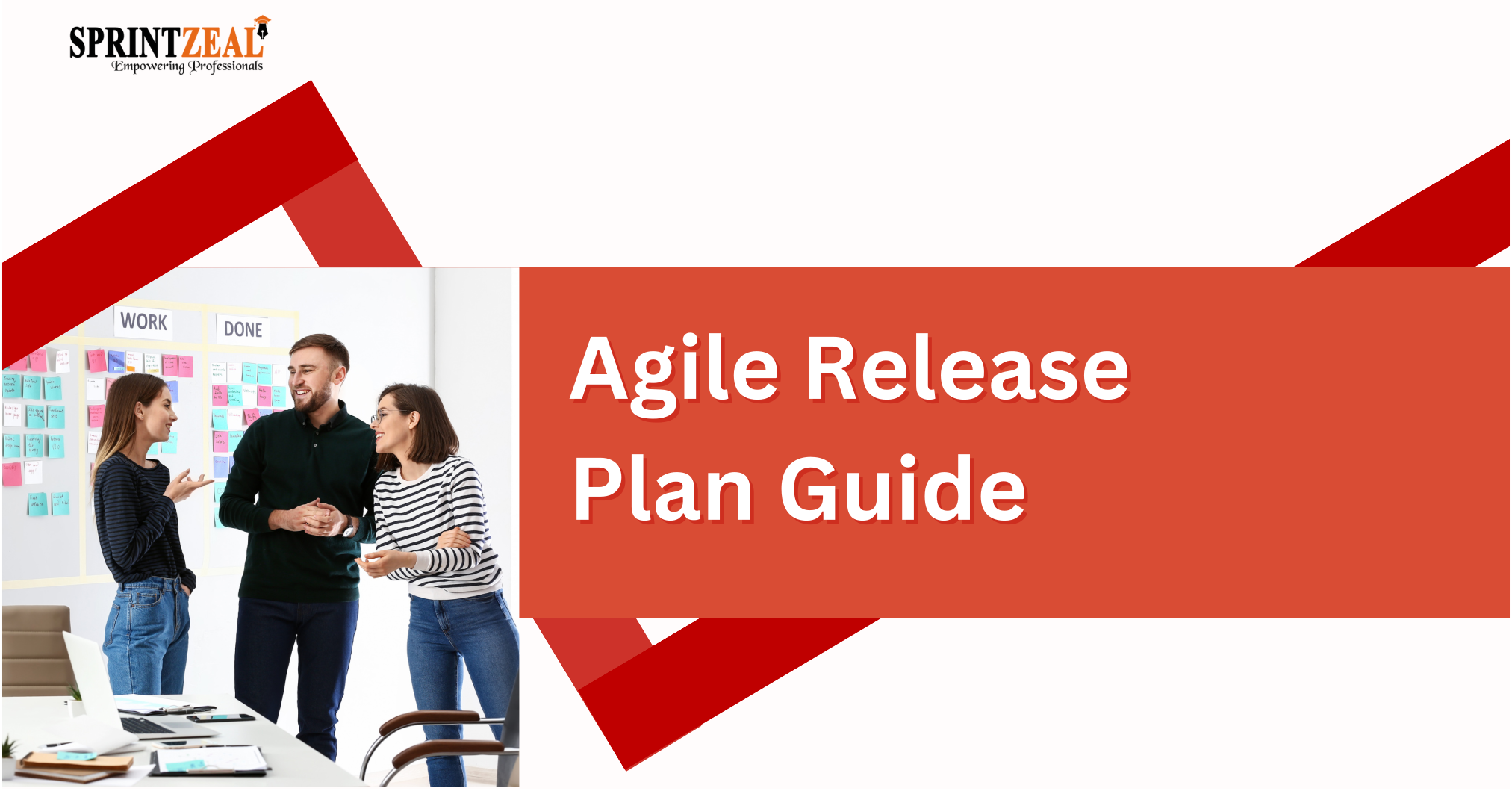
Agile Release Plan Guide
Last updated on May 9 2023
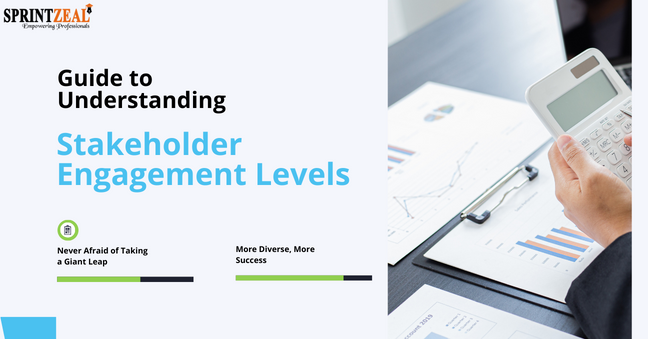
Stakeholder Engagement Levels Guide
Last updated on Sep 16 2024
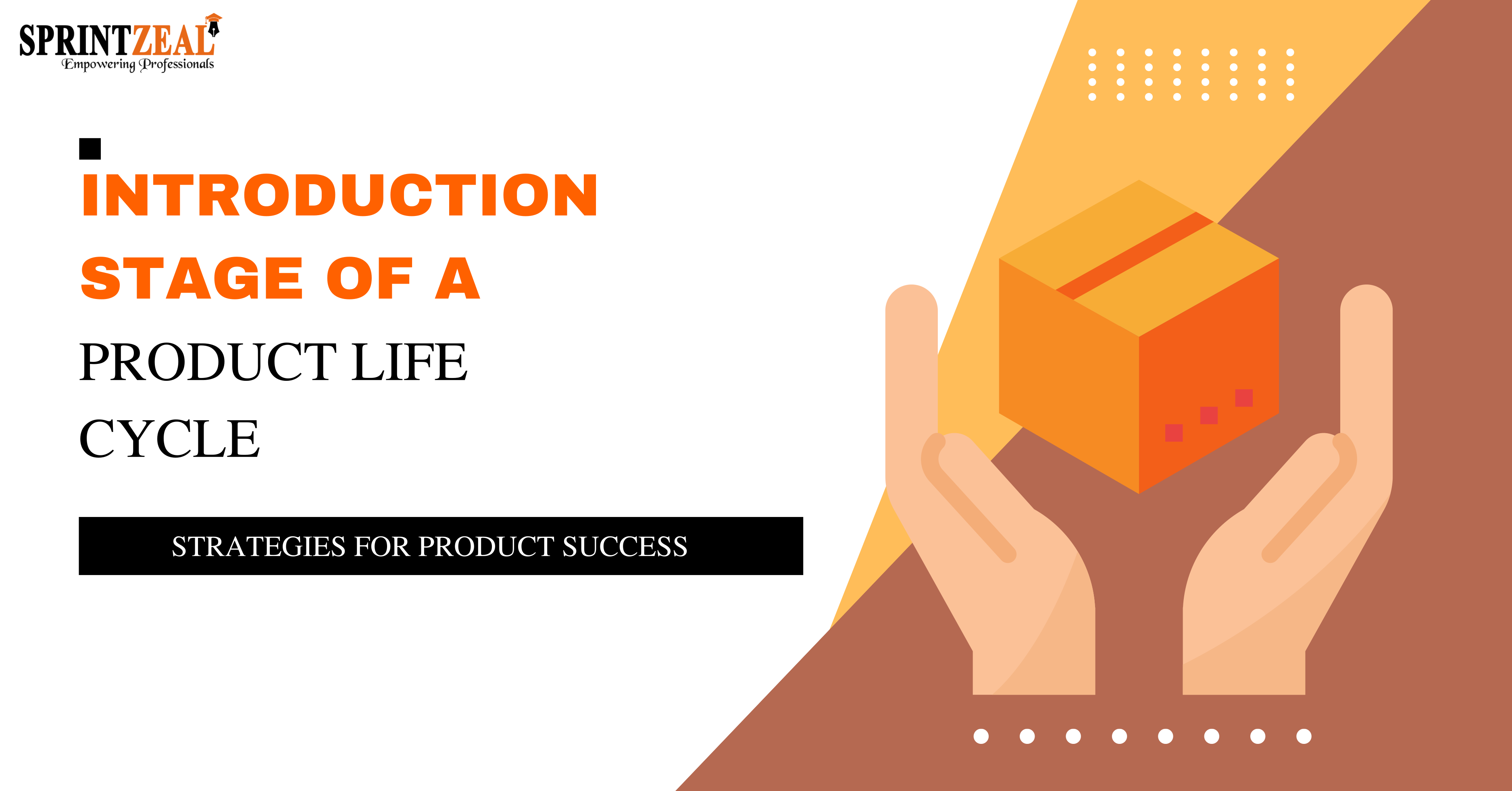
Successful Product Strategies for Introduction Stage of Product Life Cycle
Last updated on Oct 19 2023
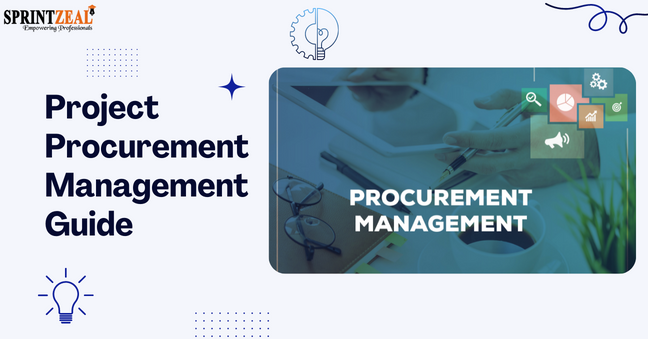
Project Procurement Management Guide
Last updated on Aug 16 2022
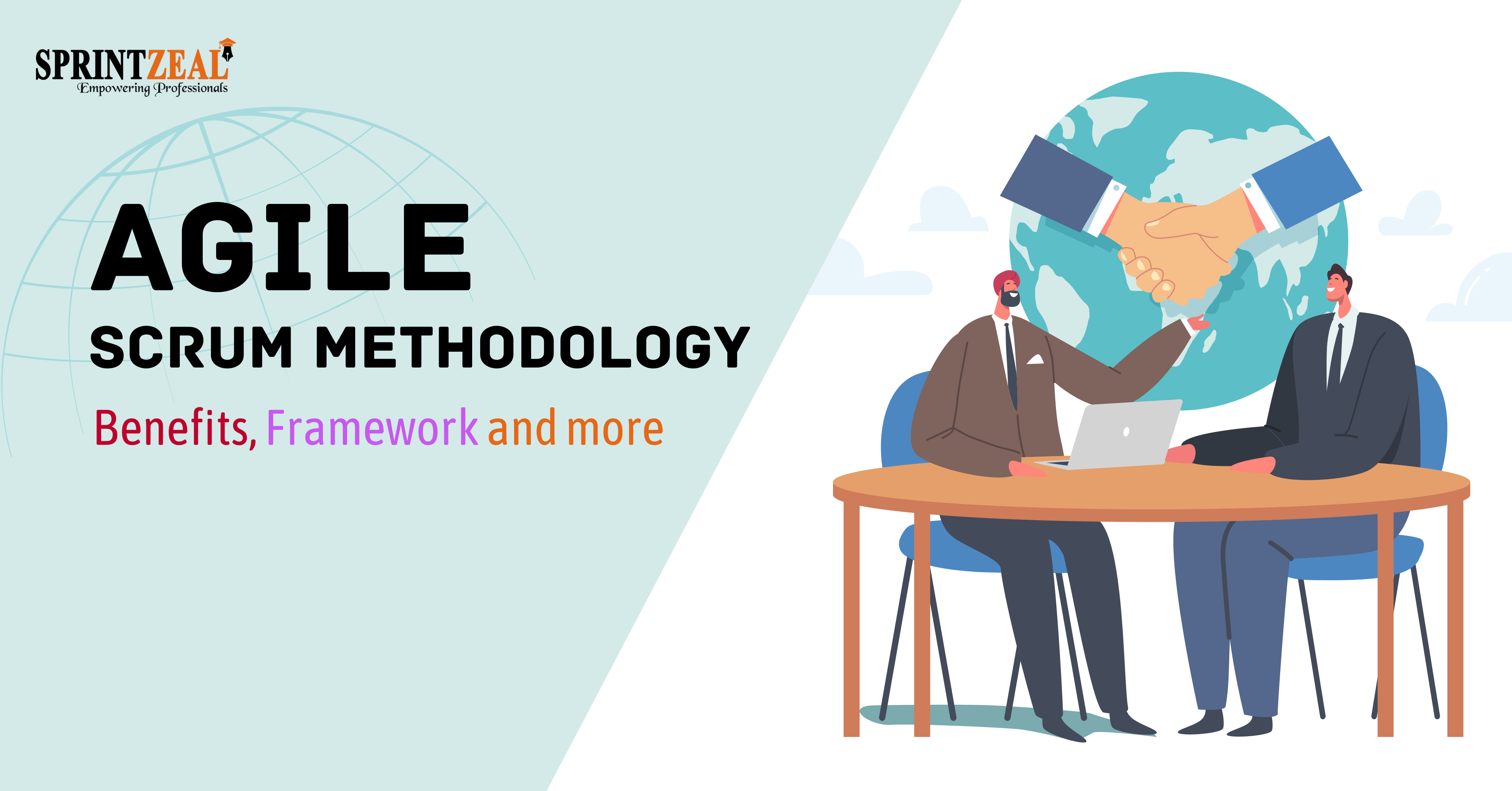
Agile Scrum Methodology - Benefits, Framework and Activities Explained
Last updated on Mar 25 2024
- Agile Management 58
- AI and Machine Learning 35
- Big Data 53
- Business Management 39
- Cloud Computing 41
- Digital Marketing 53
- Information Security 7
- IT Hardware and Networking 13
- IT Security 87
- IT Service Management 29
- Microsoft Program 2
- Programming Language 29
- Project Management 147
- Quality Management 70
- Risk Management 8
- Workplace Skill Building 1
Trending Now
List Of Traits An Effective Agile Scrum Master Must Possess
DevOps Vs Agile Differences Explained
Devops Tools Usage, and Benefits of Development Operations & VSTS
Guide to Agile Project Management 2024
10 best practices for effective DevOps in 2024
Guide to Becoming a Certified Scrum Master in 2024
Why Should You Consider Getting a Scrum Master Certification?
CSM vs CSPO: Which Certification is Right for You?
Agile Manifesto - Principles, Values and Benefits
Agile Methodology Explained in Detail
Agile Project Management Explained
Essential Tools for Agile Project Management 2024
Everything about Scrum Methodology
Career Benefits of CISM Certification in 2024
Scrum Workflow - A Step by Step Guide
Latest Agile Interview Questions and Answers To Look For In 2024
Scrum Interview Questions and Answers 2024
Top Scrum Master Responsibilities 2024 (Updated)
Product Life Cycle in Marketing: Essential Strategies for Product’s Success
DevOps Engineer - Career path, Job scope, and Certifications
Business Agility Guide - Importance, Benefits and Tips
Scrum vs Safe – Differences Explained
CSM vs. PSM - Which Scrum Certification is Better?
SAFe Implementation Roadmap Guide
Agile Environment Guide
Agile Coaching Guide - Best Skills for Agile Coaches
Agile Principles Guide
SAFe Certifications List - Best of 2024
Agile Prioritization Techniques Explained
Project Risk Management Guide
Scrum Ceremonies Guide
Product Owner Certifications List
Scrum of Scrums Guide
Project Integration Management Guide
What is DevSecOps and its Importance
Data Processing - A Beginner's Guide
DevOps Career Guide 2024
Scrum Master Career Path Explained
Scrum Career Path Explained
Project Quality Management Guide
Project Resource Management Guide
Top Git Interview Questions and Answers [Updated 2024]
A guide to Agility in cloud computing
Product Roadmap: An Ultimate Guide to Successful Planning and Implementation
DMAIC Methodology - The Ultimate Guide
Product Life Cycle Strategies: Key to Maximizing Product Efficiency
Scrum Master Salary Trends in 2024
Product Life Cycle Model: A Guide to Understanding Your Product's Success
What is a Product Owner - Role, Objectives and Importance Explained
Unlocking Career Opportunities in Product Management: Your Roadmap to Success
Saturation Stage of Product Life Cycle: Complete Guide

- Corporate Partners
- AffiliateProgram
- Cities We Serve
QUICK LINKS
- Terms & Conditions
- Privacy Policy
- Cookie Policy
- Become an Instructor
- Sprintzeal Reviews
- Past Performance Report
SECURE PAYMENTS

Top Trending Courses
People also bought.
© 2024 Sprintzeal Americas Inc. - All Rights Reserved.
- PMP, PMI, PMBOK, CAPM, PgMP, PfMP, ACP, PBA, RMP and SP are registered marks of the Project Management Institute, Inc.
- CBAP® - Is a registered trade mark of IIBA.
- ITIL® is a registered trade mark of AXELOS Limited, used under permission of AXELOS Limited. The Swirl logoTM is a trademark of AXELOS Limited, used under permission of AXELOS Limited. All rights reserved
- PRINCE2® is a registered trade mark of AXELOS Limited, used under permission of AXELOS Limited. The Swirl logoTM is a trademark of AXELOS Limited, used under permission of AXELOS Limited. All rights reserved
- Certified ScrumMaster® (CSM) and Certified Scrum Trainer® (CST) are registered trademarks of SCRUM ALLIANCE®
- Professional Scrum Master is a registered trademark of Scrum.org
- The APMG-International Finance for Non-Financial Managers and Swirl Device logo is a trade mark of The APM Group Limited.
- The Open Group®, TOGAF® are trademarks of The Open Group.
- IIBA®, the IIBA® logo, BABOK® and Business Analysis Body of Knowledge® are registered trademarks owned by International Institute of Business Analysis.
- CBAP® is a registered certification mark owned by International Institute of Business Analysis. Certified Business Analysis Professional, EEP and the EEP logo are trademarks owned by International Institute of Business Analysis..
- COBIT® is a trademark of ISACA® registered in the United States and other countries.
- CISA® is a Registered Trade Mark of the Information Systems Audit and Control Association (ISACA) and the IT Governance Institute.
- CISSP® is a registered mark of The International Information Systems Security Certification Consortium ((ISC)2).
- CompTIA A+, CompTIA Network+, CompTIA Security+ are registered marks of CompTIA Inc
- CISCO®, CCNA®, and CCNP® are trademarks of Cisco and registered trademarks in the United States and certain other countries.
- CSM®, CSPO®, CSD®, CSP®, A-CSPO®, A-CSM® are registered trademarks of Scrum Alliance®
- TOGAF® is a registered trademark of The Open Group in the United States and other countries
- All the online courses are accredited by respective governing bodies and belong to their respective owners.
- Call us on +1 833 636 6366
- Request a callback
- Mail Your Queries
Enquire Now for Up to 30% Off!
WHO WILL BE FUNDING THE COURSE?
The Easy Guide to Solving Problems with Six Sigma DMAIC Method

The most commonly used methodology in Six Sigma is the DMAIC process. Many use it to solve problems and identify and fix errors in business and manufacturing processes.
In this post, we will look at how to use the DMAIC process to solve problems. You will also find useful and editable templates that you can use right away when implementing DMAIC problem-solving in your organization.
- What are 5 the Steps of Six Sigma
DMAIC Process and Problem-Solving
Common mistakes to avoid when using six sigma dmaic methodology, how to use the dmaic methodology for problem solving in project management, what are the 5 steps of six sigma.
DMAIC is one of the core methodologies used within the Six Sigma framework. It is a data-driven method used to systematically improve the process. The approach aims to increase the quality of a product or service by focusing on optimizing the process that produces the output. This way DMAIC seeks to provide permanent solutions when it comes to process improvement.
It provides a structured problem-solving framework to identify, analyze, and improve existing processes. DMAIC guides practitioners through a series of steps to identify the root causes of process issues, implement solutions, and sustain the improvements over time.
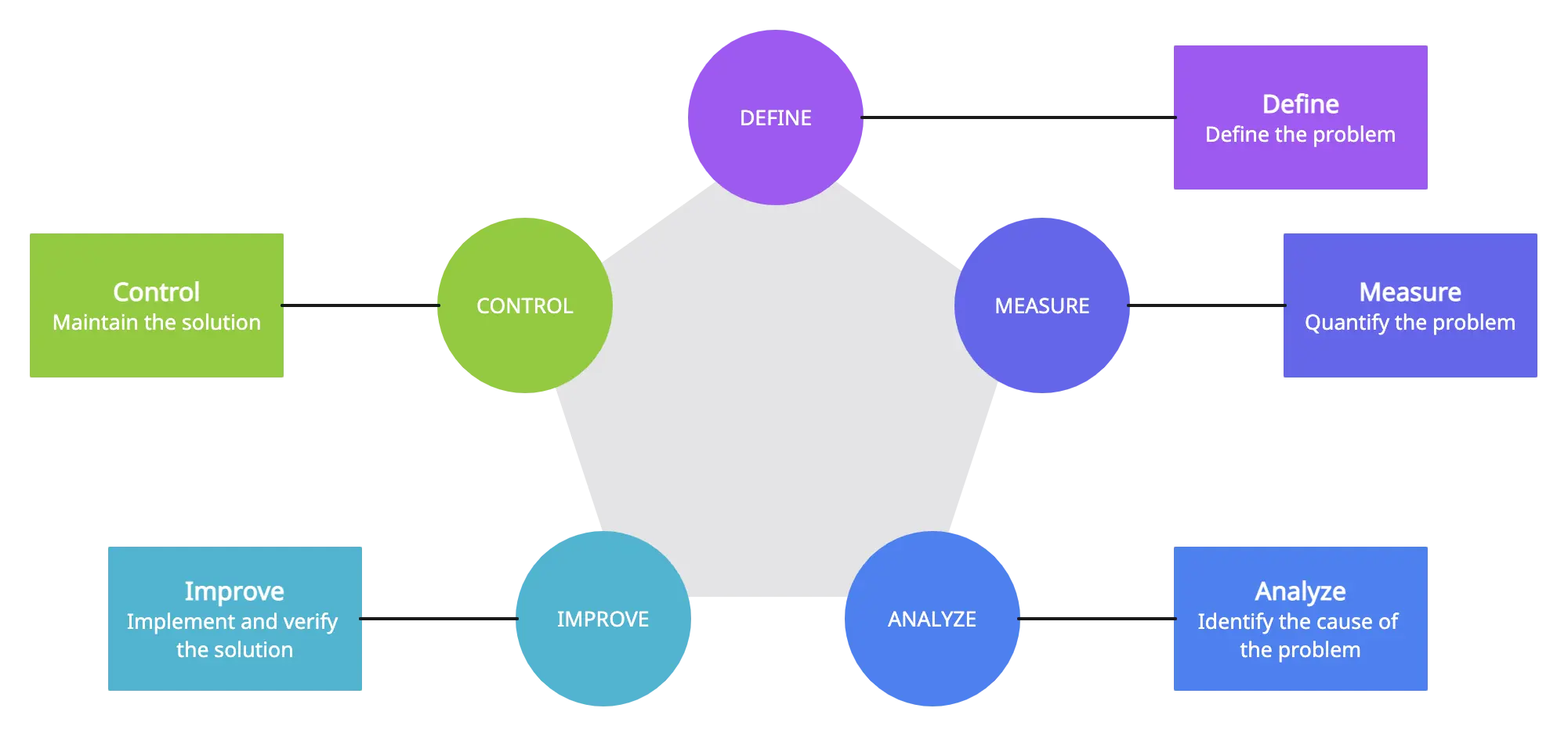
Following we have listed down the 5 phases of the DMAIC process along with the steps you need to take when using it to solve problems. Different tools for each phase is provided with editable templates.
Step 1: Define the Problem
So there’s a problem that affects your customer or your company processes. In this first step of the DMAIC problem solving method , you need to focus on what the problem is and how it has affected you as a company.
There are a few steps you need to follow in this phase.
• Create a problem statement which should include a definition of the problem in quantifiable terms and the severity of the problem.
• Make sure necessary resources such as a team leader and competent team members, and funds etc. are available at hand.
• Develop a goal statement based on your problem statement. It should be a measurable and time-bound target to achieve.
• Create a SIPOC diagram which will provide the team with a high-level overview of the process (along with its inputs, outputs, suppliers, and customers) that is being analyzed. You can also use a value stream map to do the same job.
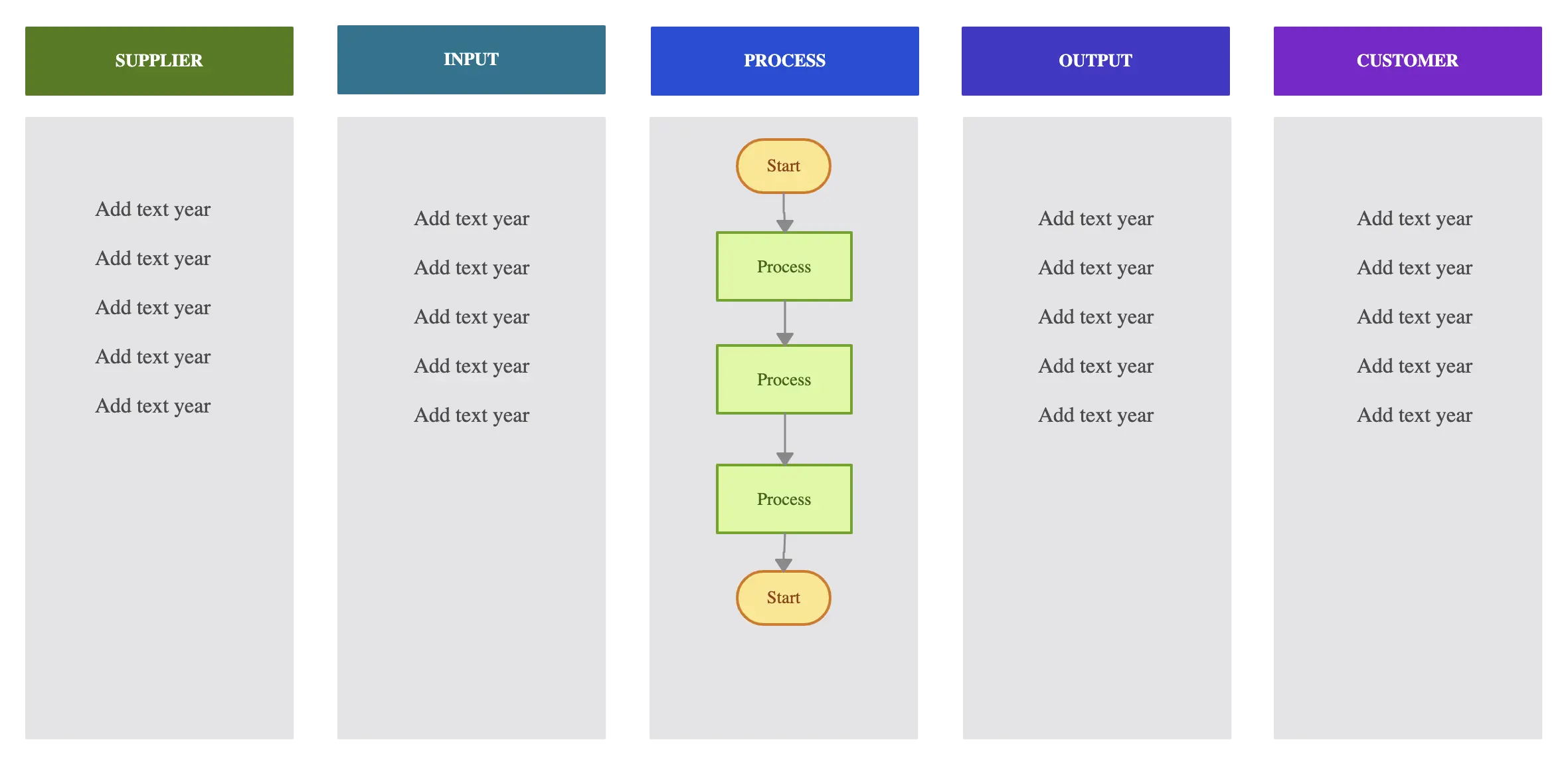
• Try to understand the process in more in-depth detail by creating a process map that outlines all process steps. Involve the process owners when identifying the process steps and developing the map. You can add swimlanes to represent different departments and actors responsible.
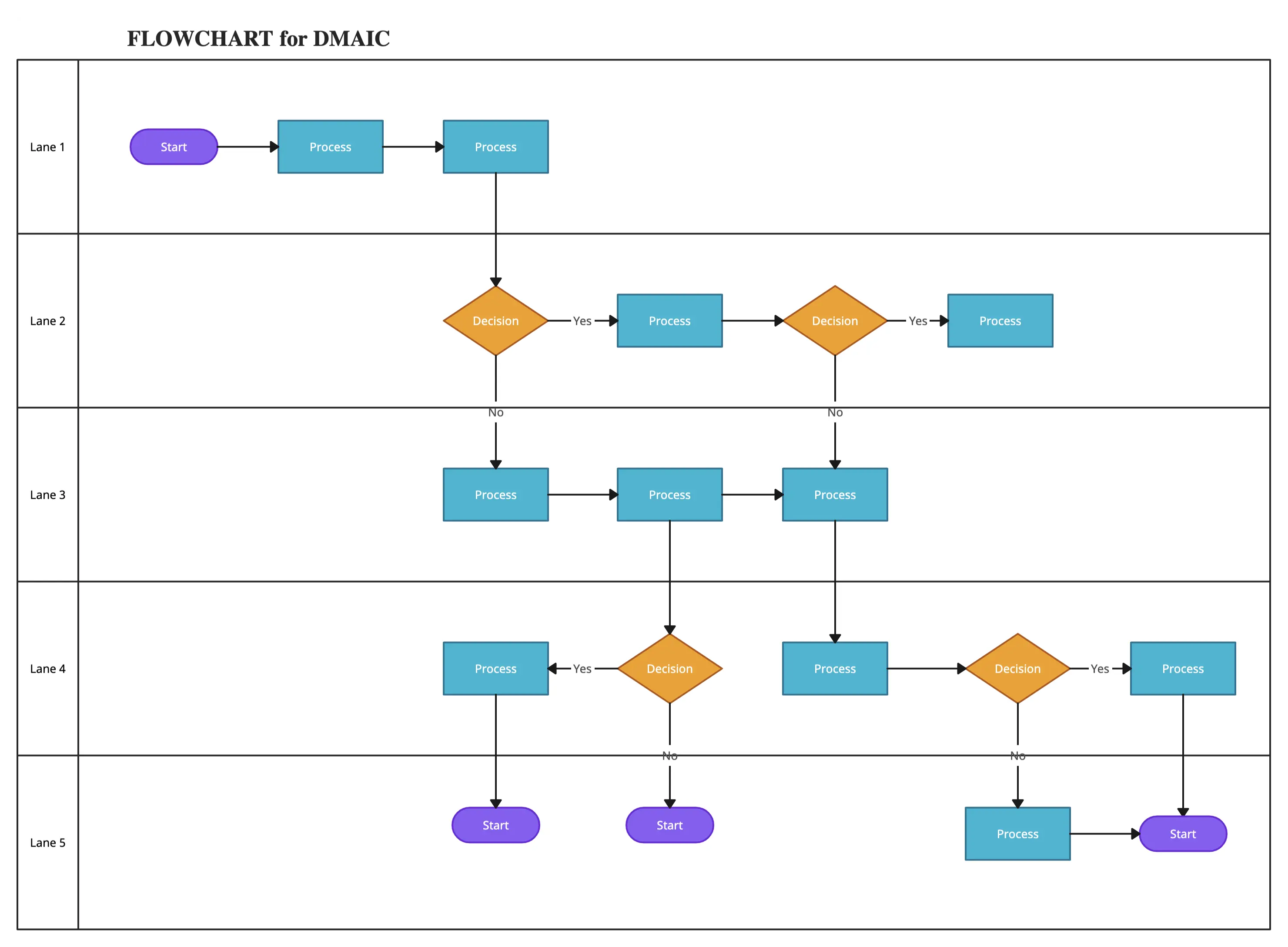
Step 2: Measure the Problem
In this step, you should measure the extent of the problem. To do so you need to examine the process in its current state to see how it performs. The detailed process map you created in the ‘Define’ phase can help you with this.
The baseline measurements you will need to look into in this phase, are process duration, the number of defects, costs and other relevant metrics.
These baseline measurements will be used as the standards against which the team will measure their success in the ‘Improve’ phase.
Step 3: Analyze the Problem
The analyze phase of the DMAIC process is about identifying the root cause that is causing the problem.
• Referring to the process maps and value stream maps you have created, further, analyze the process to identify the problem areas.
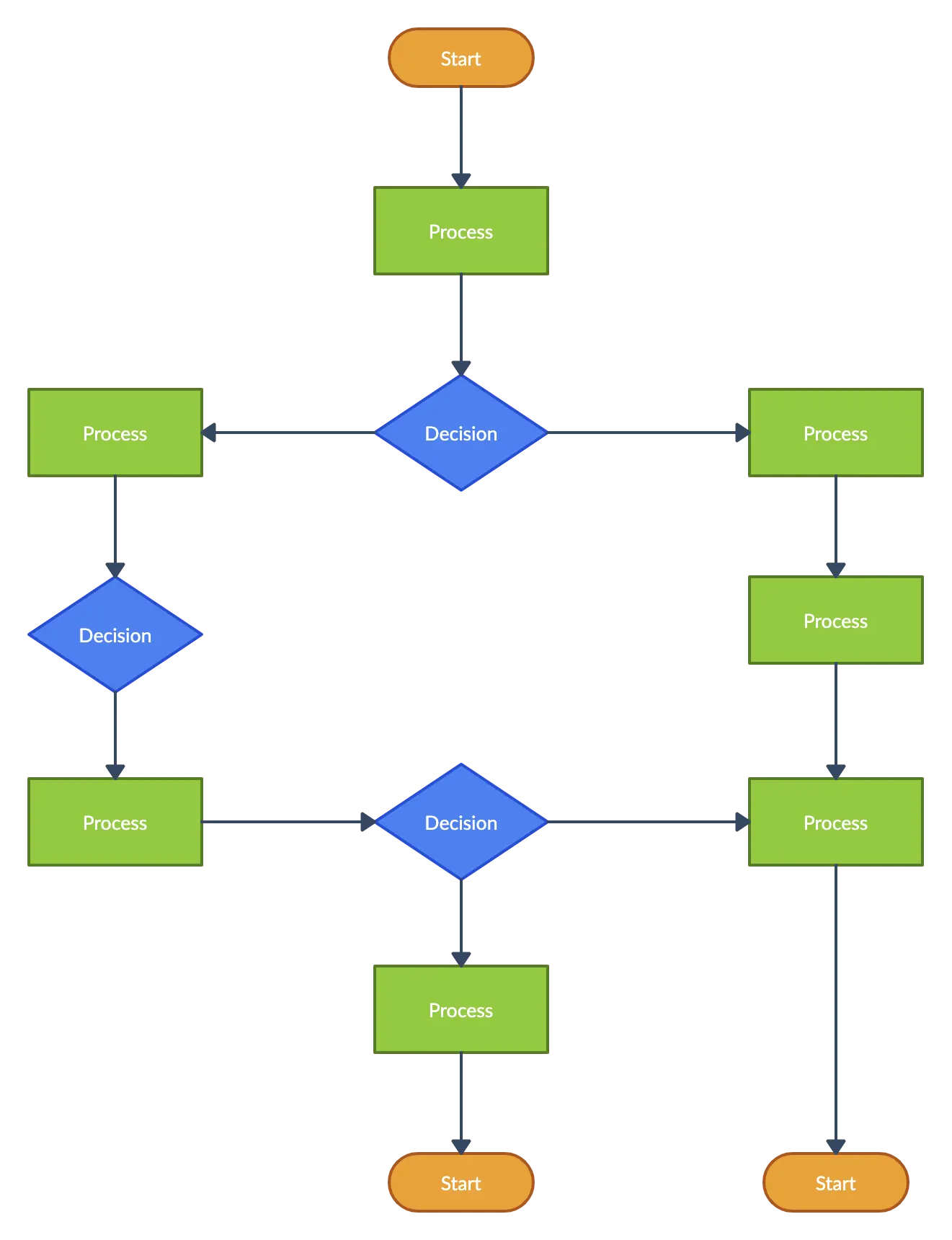
• Visualize the data you have collected (both in the ‘Measure’ phase and the analyze phase) to identify signs of problems in the processes.
• Use Pareto charts, histograms, run charts etc. to represent numerical data. Study them with team leaders and process owners to identify patterns.
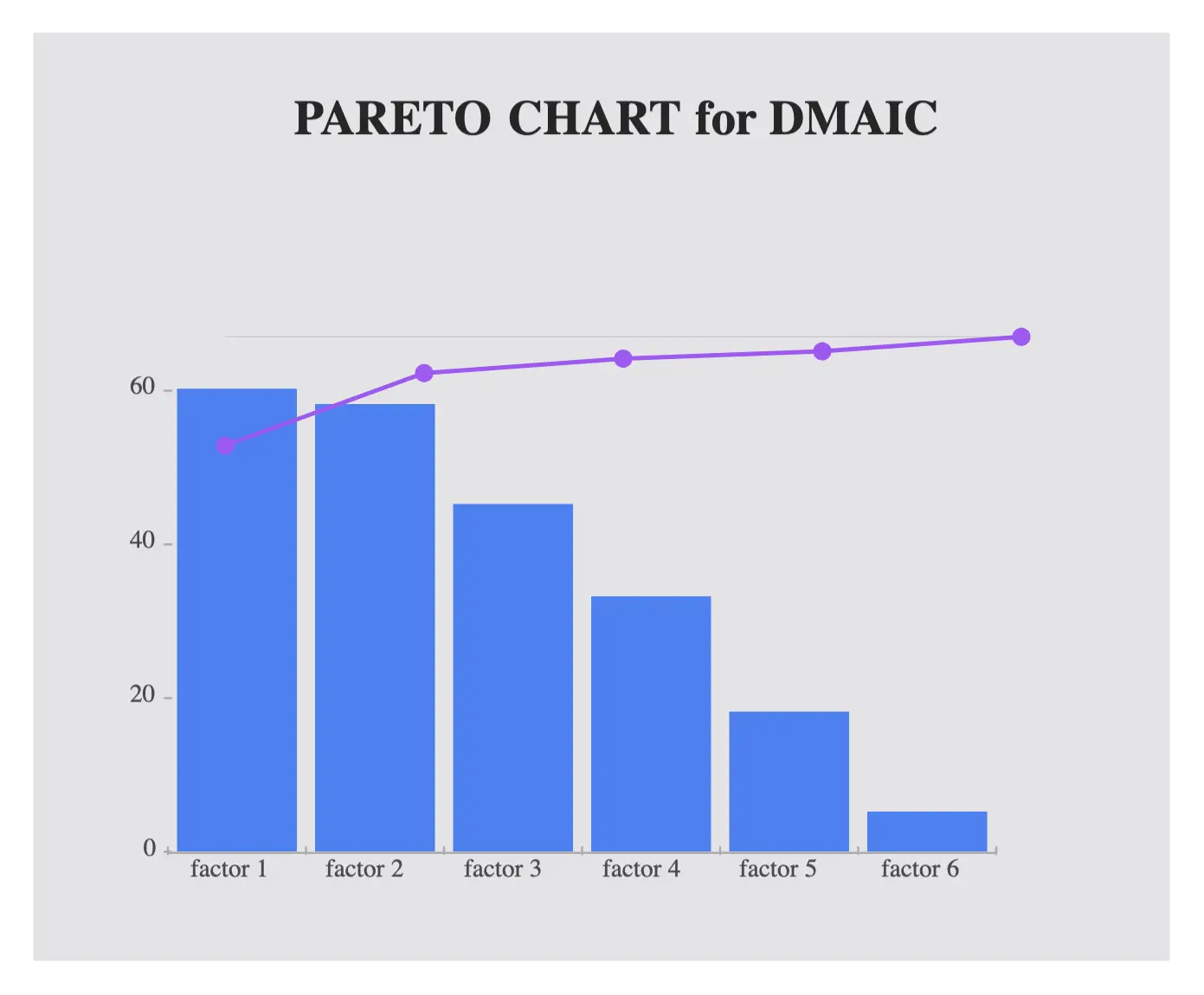
• With the results of your process analysis and your data analysis, start brainstorming the root causes of the problem. Use a cause and effect diagram/ fishbone diagram to capture the knowledge of the process participants during the session.
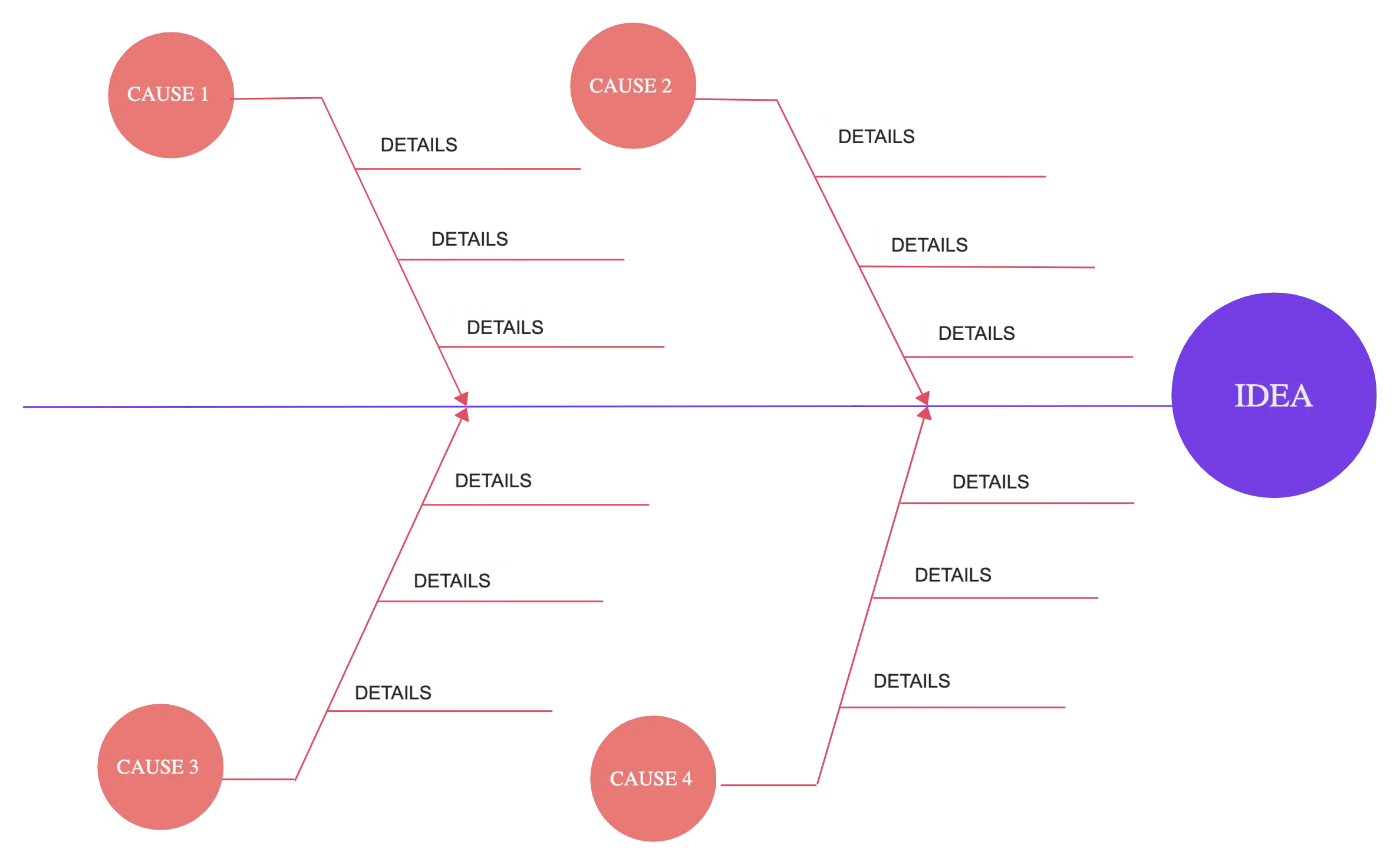
• Using a 5 whys diagram, narrow down your findings to the last few causes of the problem in your process.
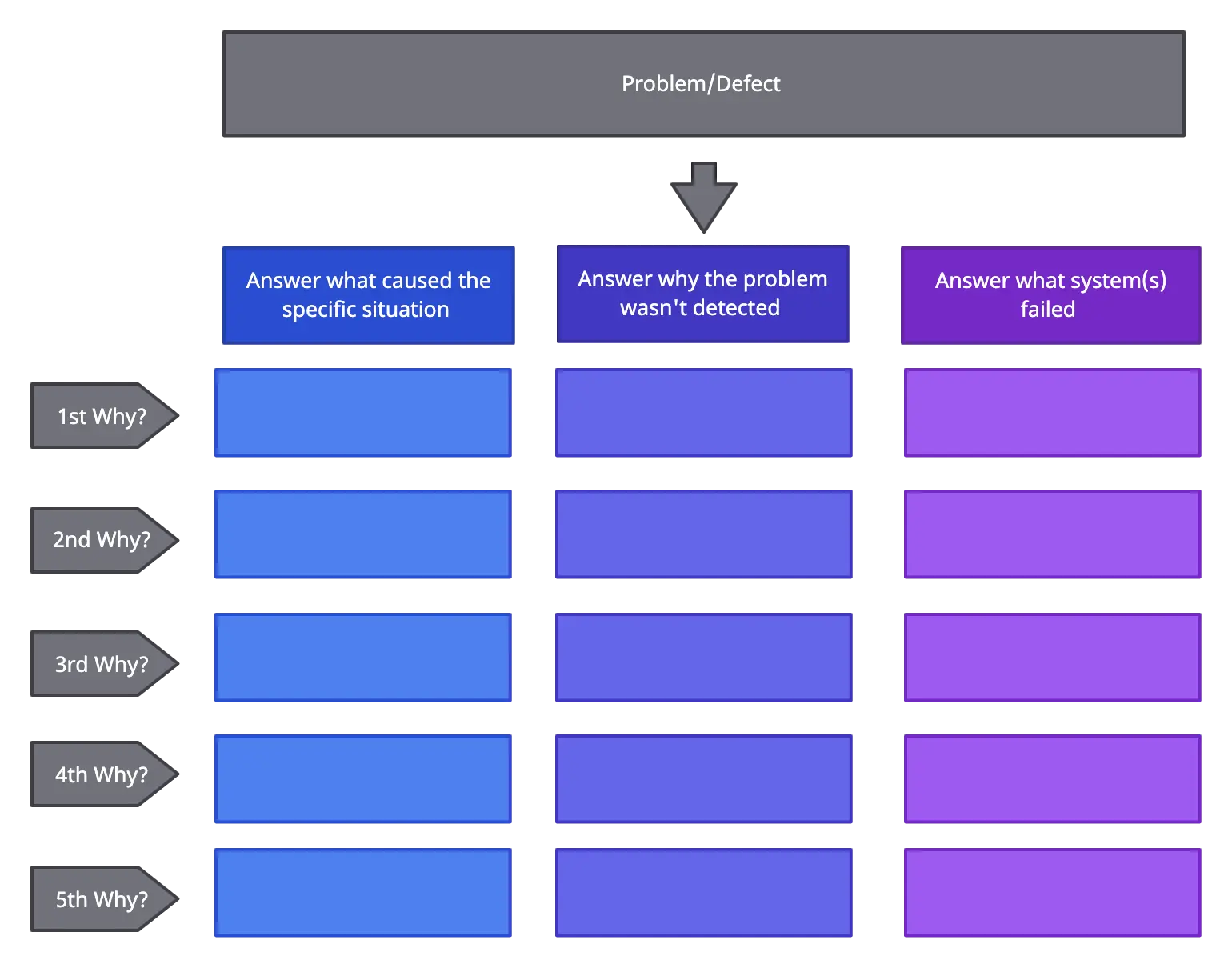
Step 4: Improve (Solve the Problem)
In this phase, the focus is on mitigating the root cause identified and brainstorming and implementing solutions. The team will also collect data to measure their improvement against the data collected during the ‘Measure’ phase.
• You may generate several effective solutions to the root cause, but implementing them all would not be practical. Therefore, you will have to select the most practical solutions.
To do this you can use an impact effort matrix . It will help you determine which solution has the best impact and the least effort/ cost.
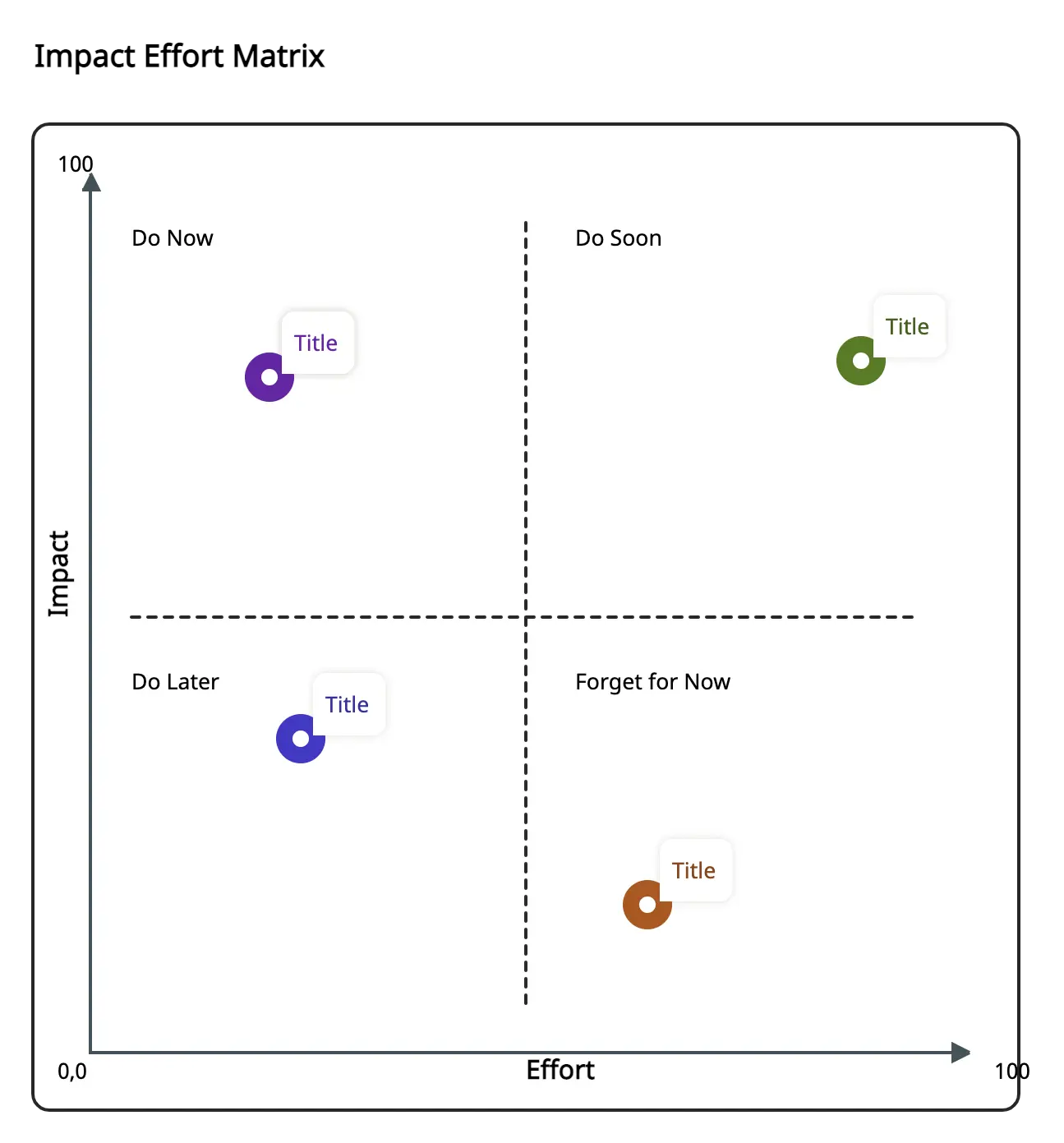
• Based on different solutions, you should develop new maps that will reflect the status of the process once the solution has been applied. This map is known as the to-be map or the future-state map. It will provide guidance for the team as they implement changes.
• Explore the different solutions using the PDCA cycle and select the best one to implement. The cycle allows you to systematically study the possible solutions, evaluate the results and select the ones that have a higher chance of success.
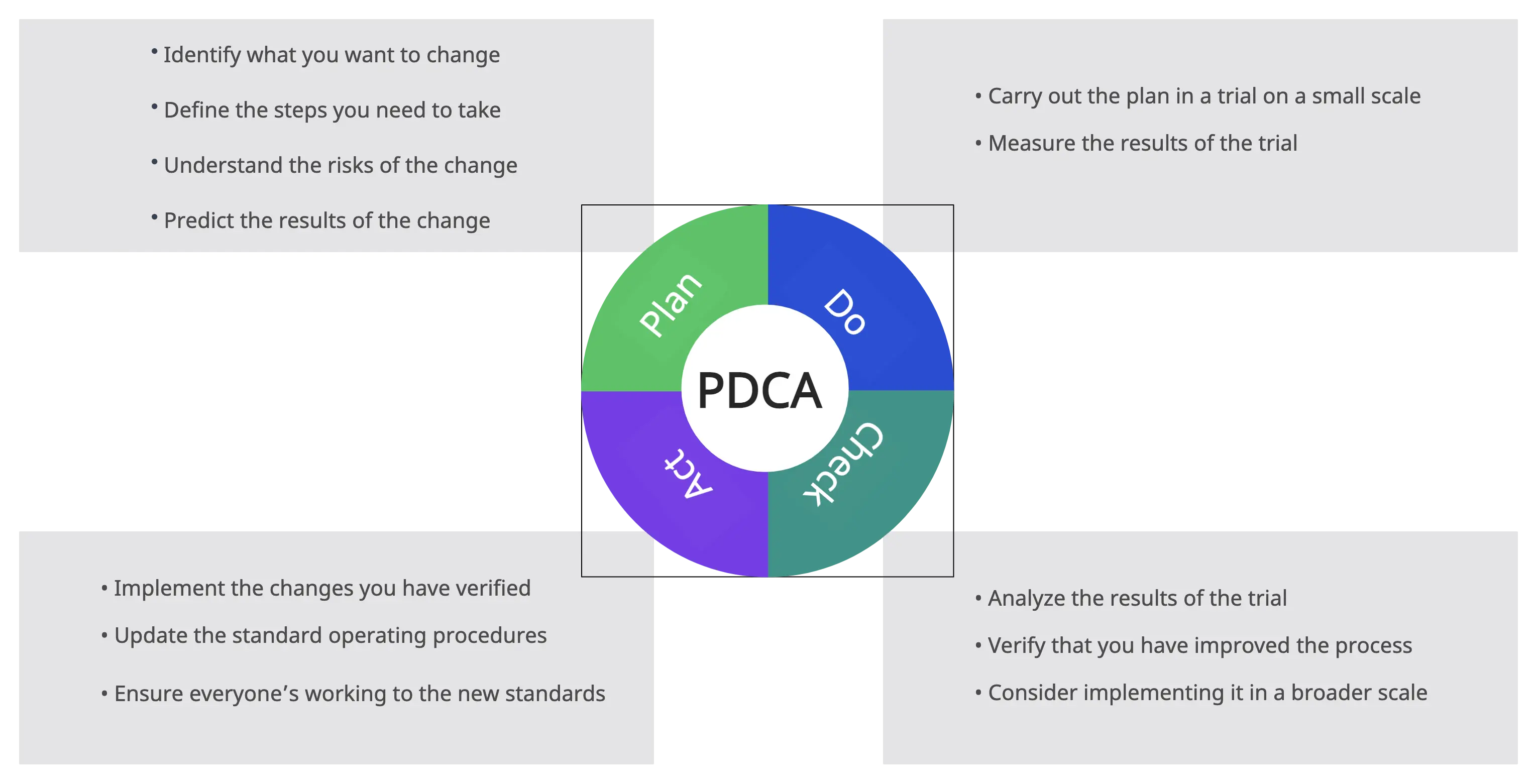
Step 5: Control (Sustain the Improvements)
In the final phase of the DMAIC method , the focus falls on maintaining the improvements you have gained by implementing the solutions. Here you should continue to measure the success and create a plan to monitor the improvements (a Monitoring plan).
You should also create a Response plan which includes steps to take if there’s a drop in the process performance. With new process maps and other documentation, you should then proceed to document the improved processes.
Hand these documents along with the Monitoring plan and the response plan to the process owners for their reference.
Insufficiently defining the problem can lead to a lack of clarity regarding the problem statement, objectives, and scope. Take the time to clearly define the problem, understand the desired outcomes, and align stakeholders' expectations.
Failing to engage key stakeholders throughout the DMAIC process can result in limited buy-in and resistance to change. Ensure that stakeholders are involved from the beginning, seeking their input, addressing concerns, and keeping them informed about progress and outcomes.
Collecting insufficient or inaccurate data can lead to flawed analysis and incorrect conclusions. Take the time to gather relevant data using appropriate measurement systems, ensure data accuracy and reliability, and apply appropriate statistical analysis techniques to derive meaningful insights.
Getting caught up in analysis paralysis without taking action is a common pitfall. While analysis is crucial, it’s equally important to translate insights into concrete improvement actions. Strive for a balance between analysis and implementation to drive real change.
Failing to test potential solutions before implementation can lead to unintended consequences. Utilize methods such as pilot studies, simulation, or small-scale experiments to validate and refine proposed solutions before full-scale implementation.
Successful process improvement is not just about making initial changes ; it’s about sustaining those improvements over the long term. Develop robust control plans, standard operating procedures, and monitoring mechanisms to ensure the gains achieved are maintained and deviations are identified and corrected.
Applying DMAIC in a one-size-fits-all manner without considering the organization’s unique culture, context, and capabilities can hinder success. Tailor the approach to fit the specific needs, capabilities, and culture of the organization to enhance acceptance and implementation.
In the project management context, the Define phase involves clearly defining the project objectives, scope, deliverables, and success criteria. It entails identifying project stakeholders, understanding their expectations, and establishing a project charter or a similar document that outlines the project’s purpose and key parameters.
The Measure phase focuses on collecting data and metrics to assess the project’s progress, performance, and adherence to schedule and budget. Key project metrics such as schedule variance, cost variance, and resource utilization are tracked and analyzed. This phase provides insights into the project’s current state and helps identify areas that require improvement.
The Analyze phase involves analyzing the project data and identifying root causes of any performance gaps or issues. It aims to understand why certain project aspects are not meeting expectations. Techniques such as root cause analysis, Pareto charts, or fishbone diagrams can be used to identify factors impacting project performance.
In the Improve phase, potential solutions and actions are developed and implemented to address the identified issues. This may involve making adjustments to the project plan, reallocating resources, refining processes, or implementing corrective measures. The goal is to optimize project performance and achieve desired outcomes.
The Control phase focuses on monitoring and controlling project activities to sustain the improvements made. It involves implementing project control mechanisms, establishing performance metrics, and conducting regular reviews to ensure that the project remains on track. Control measures help prevent deviations from the plan and enable timely corrective actions.
What are Your Thoughts on DMAIC Problem Solving Method?
Here we have covered the 5 phases of Six Sigma DMAIC and the tools that you can use in each stage. You can use them to identify problem areas in your organizational processes, generate practical solutions and implement them effectively.
Have you used DMAIC process to improve processes and solve problems in your organization? Share your experience with the tool with us in the comment section below.
Also, check our post on Process Improvement Methodologies to learn about more Six Sigma and Lean tools to streamline your processes.
FAQs about Six Sigma and DMAIC Approaches
What is six sigma, what is the difference between dmaic and dmadv.
DMAIC and DMADV are two methodologies used in Six Sigma. DMAIC is employed to enhance existing processes by addressing issues and improving efficiency, while DMADV is utilized for creating new processes or products that meet specific customer needs by following a structured design and verification process.
- Used for improving existing processes
- Define, Measure, Analyze, Improve, Control
- Identifies problem areas and implements solutions
- Focuses on reducing process variation and enhancing efficiency
- Used for developing new products, services, or processes
- Define, Measure, Analyze, Design, Verify
- Emphasizes meeting customer requirements and creating innovative solutions
- Involves detailed design and verification through testing
When to Use the DMAIC Methodology?
Problem identification : When a process is not meeting desired outcomes or experiencing defects, DMAIC can be used to identify and address the root causes of the problem.
Process optimization : DMAIC provides a systematic approach to analyze and make improvements to processes by reducing waste, improving cycle time, or enhancing overall efficiency.
Continuous improvement : DMAIC is often used as part of ongoing quality management efforts. It helps organizations maintain a culture of continuous improvement by systematically identifying and addressing process issues, reducing variation, and striving for better performance.
Data-driven decision making : DMAIC relies on data collection, measurement, and analysis. It is suitable when there is sufficient data available to evaluate process performance and identify areas for improvement.
Quality control and defect reduction : DMAIC is particularly useful when the primary objective is to reduce defects, minimize errors, and enhance product or service quality. By analyzing the root causes of defects, improvements can be made to prevent their occurrence.
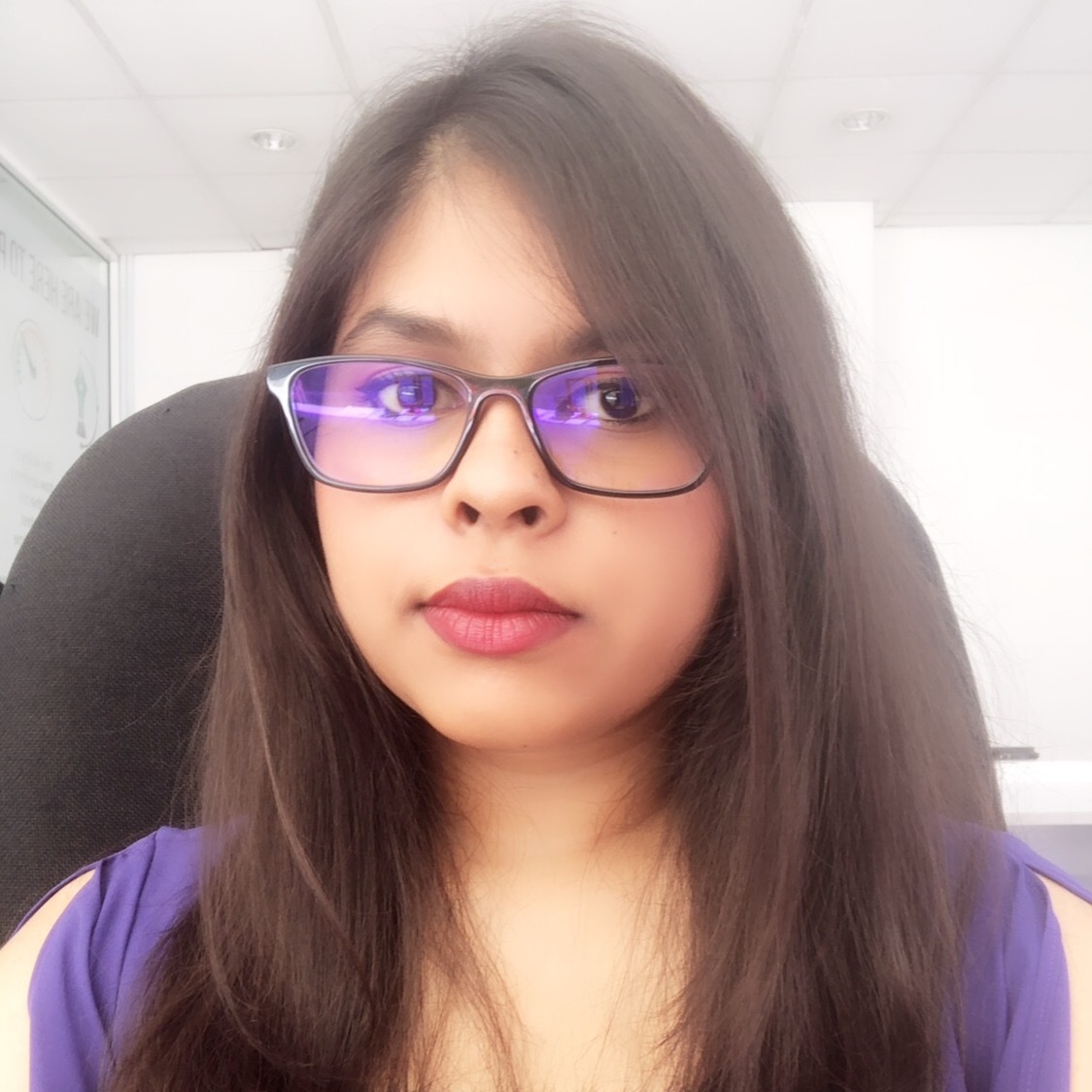
Amanda Athuraliya is the communication specialist/content writer at Creately, online diagramming and collaboration tool. She is an avid reader, a budding writer and a passionate researcher who loves to write about all kinds of topics.
Related Tools and Resources
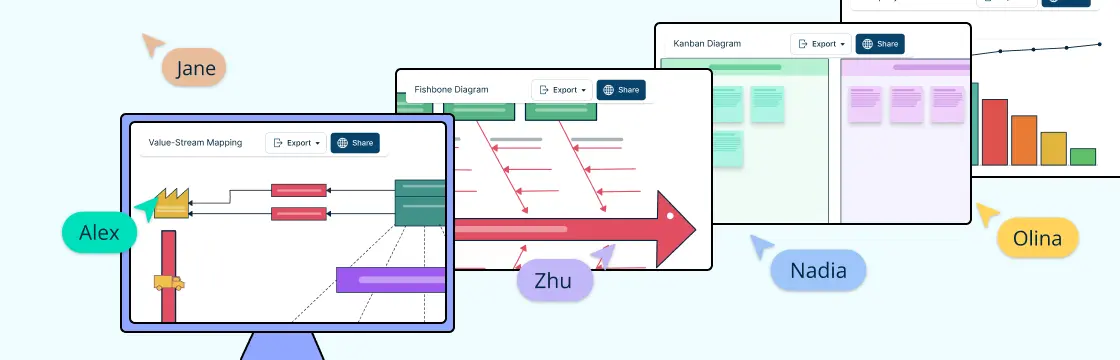
Join over thousands of organizations that use Creately to brainstorm, plan, analyze, and execute their projects successfully.
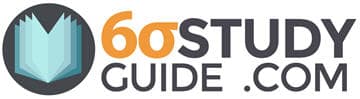
Six Sigma Study Guide
Study notes and guides for Six Sigma certification tests

DMAIC Overview
Posted by Ted Hessing
DMAIC is Six Sigma’s signature framework for process improvement. It provides a structured way of improving a process.
Key Attributes
A DMAIC improvement process:
- Is data-driven.
- Is followed in a strict sequence.
- Uses all five steps.
The Five DMAIC Stages
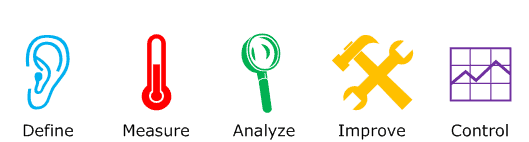
The five stages we use are:
- Define : Collate what we already know about the existing process.
- Measure : Collect further data about the existing process.
- Analyze : Identify the core problems that we’ll address.
- Improve : Plan, test, and implement solutions.
- Control : Set up supports to ensure that successful solutions are sustainable.
Note how this is reminiscent of the Deming wheel or Shewhart Wheel: Plan-Do-Study-Act ).
History of DMAIC
Michel Harry & Bill Smith created “MAIC” – the methodology that evolved to become DMAIC.
Harry includes the following strategy elements in the traditional approach to Six Sigma:
- (R) Recognize the true state of your business
- (S) Standardize the systems that prove to be best-in-class
- (I) Integrate best-in-class systems into the strategic planning framework.
What’s the difference between Six Sigma and DMAIC?
Six Sigma and DMAIC are closely related, as DMAIC is the problem-solving methodology used in Six Sigma. Six Sigma is a data-driven approach to process improvement that aims to minimize defects and variability in products and services. It uses statistical analysis and other tools to identify and eliminate the root causes of defects, and ultimately improve business performance.
DMAIC, on the other hand, is the acronym that describes the five-step problem-solving process used in Six Sigma projects. It stands for Define, Measure, Analyze, Improve, and Control. DMAIC provides a structured and disciplined approach to problem-solving that enables organizations to achieve Six Sigma levels of quality and efficiency.
Can you use DMAIC outside of Six Sigma?
Absolutely! DMAIC can be used for non-Six Sigma purposes as well.
DMAIC is a structured and disciplined problem-solving methodology that can be applied to a wide range of industries and situations beyond just Six Sigma. The five steps of DMAIC (Define, Measure, Analyze, Improve, and Control) provide a framework for identifying and eliminating problems, improving processes, and achieving better outcomes.
For example, DMAIC can be used in healthcare to improve patient care processes, reduce medical errors, and increase patient satisfaction. In the software industry, DMAIC can be used to identify and fix software bugs, improve user experience, and optimize software development processes. In construction, DMAIC can be used to improve safety practices, reduce waste, and increase productivity.
The key benefit of using DMAIC outside of Six Sigma is that it provides a standardized and data-driven approach to problem-solving that can be applied in any industry or situation. By using DMAIC, organizations can identify and address the root causes of problems, improve processes, and achieve better outcomes, regardless of whether they are formally practicing Six Sigma or not.
The DMAIC Phases
Define phase.
In the Define phase, you collate a lot of information you already have available. You’ll:
- Understand the project, including its purpose and scope.
- Map the current process.
- Determine whether the process is a good candidate for DMAIC.
- Detail customer expectations.
- Estimate timelines and costs.
Should you use DMAIC?
Some projects aren’t suitable for this process. For example:
- It’s already very clear what the problem is and how to solve it.
- There’s no or little available data on the process to be improved.
- Managers and leaders do not support improvements to this process.
- The process does not directly impact key performance indicators.
- Measuring process improvements would be difficult or impossible.
Further information about the Define phase
For more information about the Define phase, the steps to go through, and the tools to use, see Define Phase (DMAIC) .
Measure Phase
You’ve mapped the existing process, understood the project, and decided that this is a good DMAIC candidate. You’ve listed customer expectations and estimated the times and costs involved.
Your next phase involves a lot of measurements. You need to have baseline figures to assess progress accurately in later phases.
During this phase, you will:
- Identify the data that you need to collect.
- Decide what measurements to use.
- Figure out what methods to use to collect your measurements.
- Determine the level of variation that you’ll be dealing with.
- Collect the data as per previous points.
Further information about the Measure phase
For more information about the Measure phase, the steps to go through, and the tools to use, see Measure Phase (DMAIC) .
Analyze Phase
In the Analyze phase, you work with the data that you collected in the Measure phase. You’ll:
- Identify defect causes.
- Analyze these to pinpoint the root cause.
Further information about the Analyze phase
For more information about the Analyze phase, the steps to go through, and the tools to use, see Analyze Phase (DMAIC) .
Improve Phase
You’ve identified the root cause of your issue in the Analyze phase. Now you need to come up with a solution. You’ll:
- Pull in people who perform or oversee the process.
- Brainstorm potential solutions.
- Determine criteria for selecting a solution.
- Weigh potential solutions against the criteria.
- Pick a solution.
- Test the chosen solution.
- Measure the results and compare them to the Measure phase data.
Further information about the Improve phase
For more information about the Improve phase, the steps to go through, and the tools to use, see Improve Phase (DMAIC) .
Control Phase
Once you’re happy that the chosen solution will improve the process, it’s time to implement the Control phase. This is where you actually implement the said solution, but there are some other tasks too:
- Document the solution.
- Collect data about how the solution is working in production.
- Put supports in place to ensure the solution is permanent, not temporary.
- Set up a plan to deal with any issues that might arise.
- Plan handover to the operations personnel.
Further information about the Control phase
For more information about the Control phase, the steps to go through, and the tools to use, see Control Phase (DMAIC) .
DMAIC Tollgate Reviews
You’ll typically review progress regularly with your sponsors. This kind of review, especially when ending one phase and moving on to the next, is called a Tollgate review.
Learn more about DMAIC tollgate reviews here.
I originally created SixSigmaStudyGuide.com to help me prepare for my own Black belt exams. Overtime I've grown the site to help tens of thousands of Six Sigma belt candidates prepare for their Green Belt & Black Belt exams. Go here to learn how to pass your Six Sigma exam the 1st time through!
Comments (8)
Is there suppose to be a “what makes a good DMAIC project” video attached?
There will be soon. We’re currently reconstructing this page to have a different organization and more details.
Can DMAIC tools or methodology can be used in FOCUS PDCA project? what tools are relevant? What tools are not relevant?
I hadn’t heard of FOCUS so thank you for mentioning it so I could look it up.
DMAIC is an offshoot of the PDCA process (As is Agile and many other frameworks) so I’m inclined to say yes, it is.
Here’s how I would see it stacking up:
Plan -> D: Define, M: Measure, A: Analyze Do – > I: Implement. Check -> C: Control. Act -> C: Control (specifically Control Plans which could be a simple process, return to Implement and do a new thing, or even return to Define / Measure / Analyze)
Thanks for the great question!
Hi, could DMAIC be used as a root cause analysis method, specifically for the resolution of failures/problems/deviations not necessarily generated in a project but by normal operations within a process?
Hi Jennifer,
DMAIC is an acronym for the framework (Define, Measure, Analyze, Improve, Control). Root cause analysis is one step inside the Analysis phase.
I just wanted to let you know that while studying for my Green Belt in Six Sigma I have found this an invaluable resource that has demystified the whole concept of lean and DMAIC! I work in the intellectual disability sector where it is not the norm to apply lean / DMAIC to quality improvement, but where it absolutely can be applied to great effect. Thanks and kind regards, Emer
Thank you so much for the kind words, Emer! We work hard to make these concepts clear and it’s gratifying to know it’s helpful!
I don’t want to presuppose, but you might be interested in a few articles that Jamie Garret contributed about how he applied Lean Six Sigma teaching – another field where Six Sigma is not traditionally applied.
- How Lean Six Sigma Saved my Teaching Career
- How Control Charts Made Me a Better Teacher
- How Advanced Control Charts Can Save Our Schools
Leave a Reply Cancel reply
Your email address will not be published. Required fields are marked *
This site uses Akismet to reduce spam. Learn how your comment data is processed .

- Quality Management
Home » Free Resources » »
What is DMAIC in Six Sigma? How to Use the DMAIC Model?
- Written by John Terra
- Updated on July 15, 2024
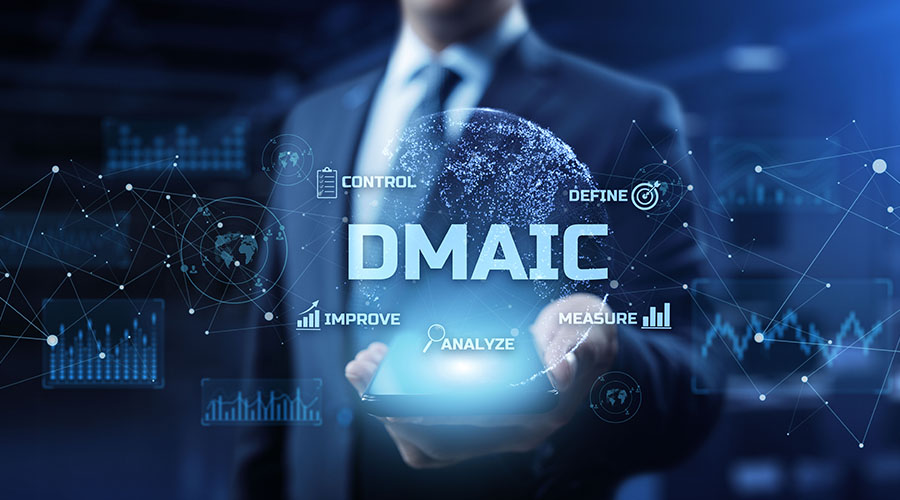
Today’s forward-thinking businesses are constantly looking for ways to improve and skilled professionals to help them achieve this. Given our current commercial atmosphere of increased competition and economic uncertainty, that’s a prudent strategy. Only companies that evolve and quickly solve problems will flourish and last.
The DMAIC model is a valuable resource that helps businesses improve performance while dealing quickly with issues. This article explains DMAIC processes, DMAIC models, DMAIC phases, and the impact of DMAIC. We’ll also share a Lean Six Sigma program that helps professionals learn how to utilize this method.
So, what’s DMAIC, anyway?
What is DMAIC?
DMAIC stands for Define, Measure, Analyze, Improve, and Control. It is a problem-solving and quality improvement methodology businesses use to improve performance. It’s a customer-focused, structured approach that also serves as a foundation for Lean Six Sigma.
Business improvement happens during the DMAIC process by taking things project by project. In this context, projects are defined as problems scheduled for solutions. The whole point of the DMAIC process is to introduce structure to problem-solving.
Some people like to shorten the term and pronounce DMIAC as “de-may-ick,” while others say “duh-may-ick.” Either way, the pronunciation issue is another example of “po-tay-to” versus “po-tah-to.”
Now, look at the classic DMAIC template based on its established steps.
Note: An effective Six Sigma Project Charter should clearly define project goals, scope, timeline, and team roles, providing a roadmap for success and effective stakeholder communication.
Also Read: What Is Process Capability and Why It’s More Interesting Than It Sounds
The DMAIC Model and its Phases
Here’s where we break down the DMAIC methodology into its distinct phases. This setup is the basis for every DMAIC template used to solve problems and improve efficiency.
The team asks, “What problem are we trying to fix?” In this first stage of the DMAIC model, Six Sigma professionals state the issue, specify the customers, outline the process, and set goals. We can subdivide this phase into:
- Identify the problem, also known as an opportunity for improvement
- Delineate the project’s scope
- Develop the client’s requirements
- Estimate the project’s impact
- Identify the project’s stakeholders
- Create the team
The team asks, “How big of an issue is this, and how does the process currently perform?” In the Measure stage, the team quantifies parameters, decides how best to measure them, gathers pertinent data, and performs the measuring by experimentation. We break down this phase as follows:
- Develop data collection methods
- Identify the input, processes, and output indicators
- Collect and analyze the current data
- Perform and finish failure modes and effects analysis
This step concerns one simple question, “What is causing the issue?” The team identifies the gaps between the desired and actual performance, determines what is causing the gaps, ascertains how process inputs affect the outputs, and ranks or prioritizes improvement opportunities. We break down the Analyze phase as follows:
- Develop the problem statement
- Write a root cause analysis
- Implement process control
- Create necessary measurable improvement experiments
- Figure out an improvement plan, sometimes called a “goal statement.”
Now we ask, “How will the project team address the root causes of the issue?” The Analyze phase identifies the issue, and the Improve phase prompts us to take action. This phase is where the team devises potential solutions, recognizes the solutions most accessible to put into action, tests likely hypothetical solutions, and then implements actual improvements:
- Discuss and generate ideas for solutions
- Determine the expected benefits of the solutions
- Develop a revised process map and related plan
- Define a pilot solution and plan
- Relay the answers to stakeholders
And finally, there is one question left, “How do we sustain the improvements?” The team must devise a detailed solution monitoring plan, watch implemented improvements for success, regularly update the plan’s records, and sustain a workable employee training process. Control is broken down into:
- Verify that failure incidents have been reduced
- Determine if additional improvements will be needed to meet the goal
- Identify and document the new work standards and procedures
- Integrate the latest strategies and share the learning experience with the appropriate parties
Although teams use the DMAIC model for Six Sigma, it shouldn’t be confused with a similar Six Sigma process known as Sigma DMADV. DMADV is an acronym standing for “define, measure, analyze, design, verify.” The Six Sigma team applies these steps to new processes to ensure they achieve the desired Six Sigma quality standards.
Note: The Central Limit Theorem is a fundamental concept in statistics. It states that the means of many independent and identically distributed random variables will be approximately normally distributed.
Also Read: Demystifying the Theory of Constraints
DMAIC Tools per Phase
There are tools that teams should use to carry out each DMAIC process phase. Here’s a quick breakdown.
- Stakeholder analysis
- Collect the customer’s voice using the VOC matrix
- Translate the voice of the customer to critical to quality (CTQ). In other words, get customer feedback and see how it translates into expectations, preferences, and dislikes.
- SIPOC diagrams/high-level process maps.
- Data Collection Plan
- Detailed Process Mapping
- Juran’s Pareto Analysis
- Value Stream Maps
- Why Analysis
- Brainstorming
- Calculating Sigma Level
- Cause and Effect Diagrams
- Failure Mode and Effect Analysis
- Graphs and Charts
- Scatter Diagrams
- Impact Control Matrix
- Stratification
- Barriers and Aids Chart
- Benchmarking
- Mistake Proofing
- Pilot Study
- Pugh Matrix
- Solution Matrix.
- Control Charts
- Process Control Plan
The Impact of the DMAIC Model
The DMAIC model is a game-changer, a valuable framework for any organization that wants to reduce waste, improve efficiency, deal with problems, and improve customer relations. Here is how the DMAIC methodology delivers a positive impact.
1) It ensures that quality thinking becomes the default way of conducting business, focusing on customers and building and sustaining customer loyalty.
2) It applies recognizable and effective quality tools to improve the organization’s goods and services and help the company achieve breakthrough performances.
3) It defines quality process performance metrics, tying them to the organization’s goals.
4) It creates a culture centered on quality that is also fun and offers a practical, measurable, and pragmatic means of achieving greater process quality levels.
5) It identifies the projects needed to drive improvements that yield sustainable results and superior quality.
The DMAIC methodology is a roadmap that keeps the team and the project moving forward efficiently. Some Six Sigma professionals refer to DMAIC as the “boss of the project” because the team’s leader, although in charge, still follows the outlined steps to complete the project and ensures that everyone on the team does so. If the team omits a step, it could prevent a business from wasting resources, devising ineffective solutions, and causing unnecessary negative culture issues.
Why Use the DMAIC Process and When Should You Use It?
Although the DMAIC process is helpful, it only fits some situations. That’s why most organizations take the extra step of determining why they think DMAIC is the correct methodology. This additional step is called “recognize.”
When evaluating the whys of the DMAIC process, consider these three factors:
- The existing process has apparent inefficiencies and defects
- There is a reasonable probability of reducing variables like lead times or other flaws while improving variables such as productivity or cost savings
- The condition is assessable; outcomes can be appropriately understood through quantifiable means.
If the above three factors apply to your situation, use DMAIC.
The Benefits of DMAIC
DMAIC offers benefits such as:
- Faster cycle times
- Improved collaboration
- Support for a culture of improvement.
- Greater impact from improvement measures.
The Differences Between DMAIC and DMADV
Both DMAIC and DMADV are part of the Lean Six Sigma philosophy. The chief difference between DMAIC and DMADV is that DMAIC improves existing processes, and DMADV emphasizes developing new processes, services, or products. So, DMAIC measures a process’s performance, while DMADV measures customer needs and specifications. Furthermore, DMADV develops business models to satisfy customer requirements, and DMAIC focuses on improving business processes by reducing and eliminating defects.
Long story short: use DMADV when launching new products or features, and use DMAIC when enhancing or improving existing products, processes, and services.
The Differences Between DMAIC and PDCA
The main difference between DMAIC and PDCA is that the former represents a data-driven improvement approach to improving, enhancing, and stabilizing business processes through five stages: Define, Measure, Analyze, Improve, and Control. Meanwhile, PDCA is a repetitive four-stage model: Plan, Do, Check, and Act, which is implemented to achieve continuous improvement in business process management.
The PDCA approach is mainly used in Lean, while DMAIC is widely utilized in Six Sigma. Also, DMAIC uses advanced statistical resources, while PDCA relies on more straightforward, simple tools.
Now, let’s check out some DMAIC examples.
Examples of DMAIC Usage
DMAIC can be used in many different industries and situations. For example:
- Evidence-Based Care Affecting Hospital Outcomes. Infections are a massive concern in hospitals, so a process like DMAIC can be used to define the problem, measure the current rate of infections, determine the underlying causes, implement a series of measures to combat infections, train and reinforce the culture among the staff, and report the successful results.
- Improving a Manufacturing Shop Floor’s Yield. Here, we’re looking at a repetitive manufacturing process. The goal is to enhance the yield. First, identify the products in question and the goals. Next, define the metrics used in the process and gather the needed data. Then, analyze the data for trends, deviations, and outliers. Once the issues have been identified, define and install countermeasures to answer the problems. Then, implement the measures to sustain improved performance. And finally, apply the process to future machines and products.
Also Read: Value Stream Mapping in Six Sigma
How Do You Use the DMAIC Model in Six Sigma?
So, how do we use the DMAIC template? An organization should follow four easy steps to implement DMAIC and start seeing positive results.
1) Training. Begin your organization’s DMAIC journey by training your team in the DMAIC methodology and how you expect it to be employed. Place a strong emphasis on the model’s data collection characteristics. After all, knowledge is power.
2) Line up your support and DMAIC tools. Since the DMAIC model is strongly associated with Lean Six Sigma, it’s not surprising that many Lean Six Sigma tools are compatible with the DMAIC life cycle. These tools include the Five Whys, fishbone diagrams, control charts, and Catchball. Decide which tools your team can use and how they will be shared and documented. Use improvement management to store all your DMAIC-related documents and progress notes.
3) Provide examples. Prevent confusion and reinforce DMAIC understanding by providing your team with examples of new or existing processes within your company that can benefit the most from DMAIC implementation. People typically grasp things faster and better if given practical application examples. Once everyone on the team understands how DMAIC can be used, create an atmosphere where it’s easy for the team members to suggest process improvement opportunities.
4) Initiate a pilot project. Now that you have gotten this far and laid the groundwork, it’s time to take DMAIC out for a quick spin. Pilot projects are initial, small-scale tests that show how the full-scale project will work in practice. So, pick a simple project that draws in people from multiple teams. This exercise helps test cross-team cooperation and collaboration, an essential element in future projects. Then, carefully monitor every cycle step and ensure each step is complete before moving on to the next.
Do You Want to Learn About Six Sigma?
Six Sigma is a proven methodology that helps businesses reach their full potential and remain relevant in today’s highly competitive marketplace. If you’re intrigued by Six Sigma and want to learn more, Simplilearn, in collaboration with the University of Massachusetts, offers a post graduate program in Six Sigma training that will sharpen your skills.
When you attend the program’s live interactive classes and work on real-world business problems via case studies and projects, you will pick up valuable Six Sigma skills like:
- Agile Management
- Digital Transformation
- Lean Management
- Lean Six Sigma Black Belt
- Lean Six Sigma Green Belt
Every course is aligned with IASSC-Lean Six Sigma and features real-world case studies and a capstone project that provides you with the real-world experience you need to master Six Sigma. Additionally, graduates earn certificates and membership in the UMass Amherst Alumni Association.
According to Salary.com , the median salary for Green Belt Lean Six Sigma professionals working in the United States is $115,800 and ranges over $128K at the high mark. So, whether you want to start a new career in Six Sigma or just upskill to enhance your skill set, this post-graduate program will undoubtedly provide you with the valuable Six Sigma training that today’s business world wants in its new candidates. Sign up today!
Q: What does DMAIC mean in Six Sigma?
A: DMAIC stands for Define, Measure, Analyze, Improve, and Control.
Q: What is the DMAIC process used for?
A: The DMAIC process is a data-driven process improvement cycle that aims to optimize, improve, and stabilize business designs and processes.
Q: How does Six Sigma use DMAIC?
A: DMAIC is a problem-solving approach that drives Lean Six Sigma. DMAIC’s five-phase method, Define, Measure, Analyze, Improve, and Control, improves existing process problems with unknown causes.
Q: What are the DMAIC tools?
A: DMAIC tools are, by phase:
- Define Phase: Project Charters, SIPOC Diagrams
- Measure Phase: Data Collection Plans, Process Mapping
- Analyze Phase: Cause-and-Effect Diagrams, Pareto Charts, Hypothesis Testing
- Improve Phase: Brainstorming, Design of Experiments (DOE)
- Control Phase: Control Charts, Standard Operating Procedures (SOPs)
Q: What is the benefit of DMAIC?
A: DMAIC offers benefits such as:
- Support for a culture of improvement
- Greater impact from improvement measures
You might also like to read:
Demystifying Kaizen Lean Six Sigma
A Deep Dive Into the Five Phases of Lean Six Sigma
Ultimate Guide to Six Sigma Control Charts
DMADV: Everything You Need to Know
Describing a SIPOC Diagram: Everything You Should Know About It
Leave a Comment Cancel Reply
Your email address will not be published. Required fields are marked *
Recommended Articles
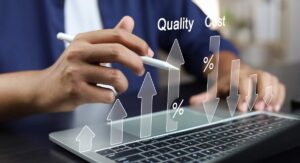
What is Quality Management in Project Management, and Why is it Critical?
Ever wondered why some projects hit all the right notes while others falter? One critical factor that often makes or breaks a project is quality
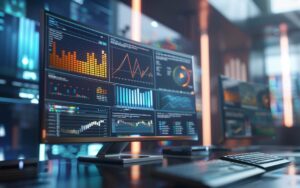
Career Tips: Top Process Improvement Tools and Methodologies to Succeed
Learn about the top process improvement tools in this beginner’s guide and how to use them to enhance efficiency and streamline operations.
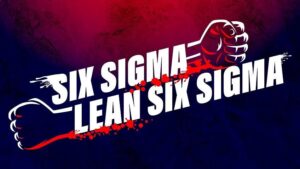

Six Sigma vs. Lean Six Sigma: Which Methodology Is Right for Your Business?
Six Sigma and Lean Six Sigma both strive to accomplish similar goals: to create more efficient processes that produce greater value. However, they approach the
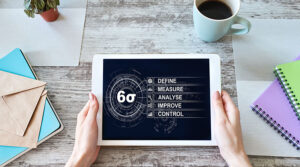
Six Sigma Methodologies for Process Improvement in 2024-25: Achieve Quality Excellence
Elevate your process improvement game in 2024 with Six Sigma methodologies. Achieve quality excellence with expert insights in this informative blog.
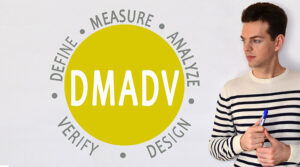
What is DMADV? Here’s Everything You Need to Know
Unlock DMADV Success: Your Complete Guide. Dive into Quality Management with UMass Boot Camp’s expert insights. Explore now!
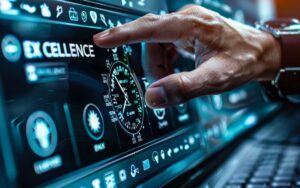
Exploring 10 Top Continuous Improvement Tools
Explore the best continuous improvement tools for 2024 that allow businesses to implement gradual changes, optimize workflows, and maintain operational stability.
Lean Six Sigma Certification
Learning Format
Online Bootcamp
Program benefits.
- Green and Black Belt exam training material included
- Aligned with IASSC-Lean Six Sigma
- Masterclasses from top faculty of UMass Amherst
- UMass Amherst Alumni Association membership
- Memberships
- Start for free
DMAIC Process explained

DMAIC process: this article explains DMAIC Process in a practical way. This article contains a general defintion of the DMAIC Process, associated steps and practical examples. After reading you will understand the basics of this Six Sigma and problem solving tool. Enjoy reading!
What is a DMAIC Process? The basics explained
The DMAIC Process is a data driven problem solving tool that can be used to improve, optimize and stabilize business processes. This cyclical problem solving model seeks to improve the processes performance within an organization. The acronym of this Lean Six Sigma tool stands for: Define, Measure, Analyse, Improve and Control.
The base of this problem solving tool is founded by Shingeo Shingo during the development of Poka Yoke .
Five basic steps of the DMAIC Process cycle
The DMAIC Process consists of five steps that match the cycle process perfectly. It is recommended to make DMAIC an integral part of every project or organization. It can be applied to any existing processes.

Figure 1 – the DMAIC Process Cycle
The problem is defined in this first step.Furthermore, it is important to recognize and define the following elements:
Your company name or product here? Ask about the possibilities More information
- who are the customers?
- what are the critical stages in the process?
- what is the objective and what are the related business processes?
The purpose of the measure phase of the DMAIC Process is to establish the most important aspects of the current process and to collect relevant data. The following aspects are important in this:
- analyse the output and the input
- define the measurement plan
- test the measurement system
Subsequently, the data that was collected in the previous step is analysed. The purpose of this step is to identify the root cause relationships. The deeper causes of defects and errors are investigated. Basic tools are used to:
- identify the gap between current and required performance
- identify the input and the output
- list and prioritize potential opportunities to improve
The current process is improved by using techniques and creative solutions. Brainstorming sessions can be a useful tool. Other, obvious solutions are:
- innovative ideas
- focus on the simplest and easiest solutions
- create a detailed implementation plan
- implementation of improvements
- identify errors and causes using an Ishikawa diagram
This step does not only focus on control but on monitoring as well. Control ensures that any deviations can be corrected in the future. Monitoring leads to sustainable improvements and guarantees long-term success. Permanent monitoring is therefore required.

Linking the DMAIC Process Cycle with business processes
To supplement the standard DMAIC Process, it is recommended to implement this step-by-step plan in other business processes as well. By sharing experiences and new knowledge with other departments, changes can be effected more easily within the entire organization.
It is important that employees have a good understanding of the usefulness of the procedure of the DMAIC process, that they discuss it with each other and that they are willing to share their experiences.
The DMAIC Process Cycle versus Six Sigma
Initially, the DMAIC process was linked to Six Sigma . Six Sigma was developed by Motorola and General Electrics to improve the quality of process outputs.
This is done by identifying and removing the causes of errors. The process is not exclusive to Six Sigma and can therefore be used to improve processes in other organizations.
Comparison of the DMAIC Process with the PDCA cycle (Deming)
DMAIC is actually an application of Deming’s PDCA cycle . The DMAIC Process takes a project based approach, whereas the PDCA cycle has a wider application.
This means it is can also be applied to one project. The DMAIC process analyses the root cause of the problem whereas the PDCA cycle focuses on the entire operation and it unearths other causes as well.
Benefits of using the DMAIC Process Cycle
The DMAIC Process is based on framework thinking within for example a product group, customer group or service. The strengths of this problem solving approach lie in the addressing and optimizing of the root causes in a process.
For a creative change in which an organization changes course completely, however, the model is less applicable. When going through the steps of the process, there may not be any overlaps. The best results are achieved with a plan-led team approach.
Example of the DMAIC Process
Let us look at a car garage with 50 locations who specialise in car tyres as an example. So far, in each branch, they have plenty of stock in various types of summer and winter tyres.
This enables them to quickly help the customer, delivering customer satisfaction and good word-of-mouth advertising. It now appears that the costs of the car company where very high last year. Management then decides to speak with all 50 branches in order to find out why.
The costs have risen sharply due to employee costs, renting space for 50 branches and inventory.
The costs are compared to that of last year and it turns out the costs are 20% higher, without creating more revenue.
Together with all 50 branches, the biggest cost item is examined. Several different factors are then identified. On average, it appears that inventory costs were 15% higher than in the previous year, among other things due to insufficient variety whereby ‘older’ models are left longer in the warehouse.
Together with the 50 branches, management looks at methods for improvement. For example, they propose to work from a central warehouse, supplying the branches 3x per week. Another option is to only have conventional tyres in stock while keeping specific tyre types in the central warehouse. The first solution is chosen unanimously.
After a test period an evaluation takes place with all branches and management. It turns out that employees have to cancel a sale more often or only help customers after a few days.
It’s Your Turn
What do you think? Is the DMAIC Methodology applicable in today’s modern economy and companies? What is your experience? What tips can you share to help others being successful in applying the DMAIC process?
Share your experience and knowledge in the comments box below.
More information
- de Mast, J., & Lokkerbol, J. (2012). An analysis of the Six Sigma DMAIC method from the perspective of problem solving . International Journal of Production Economics, 139(2), 604-614.
- Pyzdek, T., & Keller, P. A. (2003). The six sigma handbook . McGraw-Hill .
- General Electric. (2006). Six Sigma . Available at: https://www.ge.com/sixsigma/. Accessed March 7, 2006.
How to cite this article: Mulder, P. (2013). DMAIC Process . Retrieved [insert date] from Toolshero: https://www.toolshero.com/problem-solving/dmaic-process/
Original publication date: 05/28/2013 | Last update: 08/22/2023
Add a link to this page on your website: <a href=”https://www.toolshero.com/problem-solving/dmaic-process/”>toolshero: Toolshero: DMAIC Process</a>
Did you find this article interesting?
Your rating is more than welcome or share this article via Social media!
Average rating 4 / 5. Vote count: 12
No votes so far! Be the first to rate this post.
We are sorry that this post was not useful for you!
Let us improve this post!
Tell us how we can improve this post?

Patty Mulder
Patty Mulder is an Dutch expert on Management Skills, Personal Effectiveness and Business Communication. She is also a Content writer, Business Coach and Company Trainer and lives in the Netherlands (Europe). Note: all her articles are written in Dutch and we translated her articles to English!
Related ARTICLES

Deming 14 Points explained: the summary
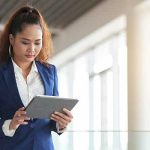
Case Management explained including certification

Inventory Count, an Inventory Management Tool: Importance and Tips

Masaaki Imai biography, quotes and books

Total Quality Management (TQM): Meaning and Explanation

Drum Buffer Rope Theory: the Concept explained
Also interesting.

PDCA Cycle by Deming: Meaning and Steps

Straw Man Proposal: The basics and template

TRIZ Method of Problem Solving explained
Leave a reply cancel reply.
You must be logged in to post a comment.
BOOST YOUR SKILLS
Toolshero supports people worldwide ( 10+ million visitors from 100+ countries ) to empower themselves through an easily accessible and high-quality learning platform for personal and professional development.
By making access to scientific knowledge simple and affordable, self-development becomes attainable for everyone, including you! Join our learning platform and boost your skills with Toolshero.

POPULAR TOPICS
- Change Management
- Marketing Theories
- Problem Solving Theories
- Psychology Theories
ABOUT TOOLSHERO
- Free Toolshero e-book
- Memberships & Pricing
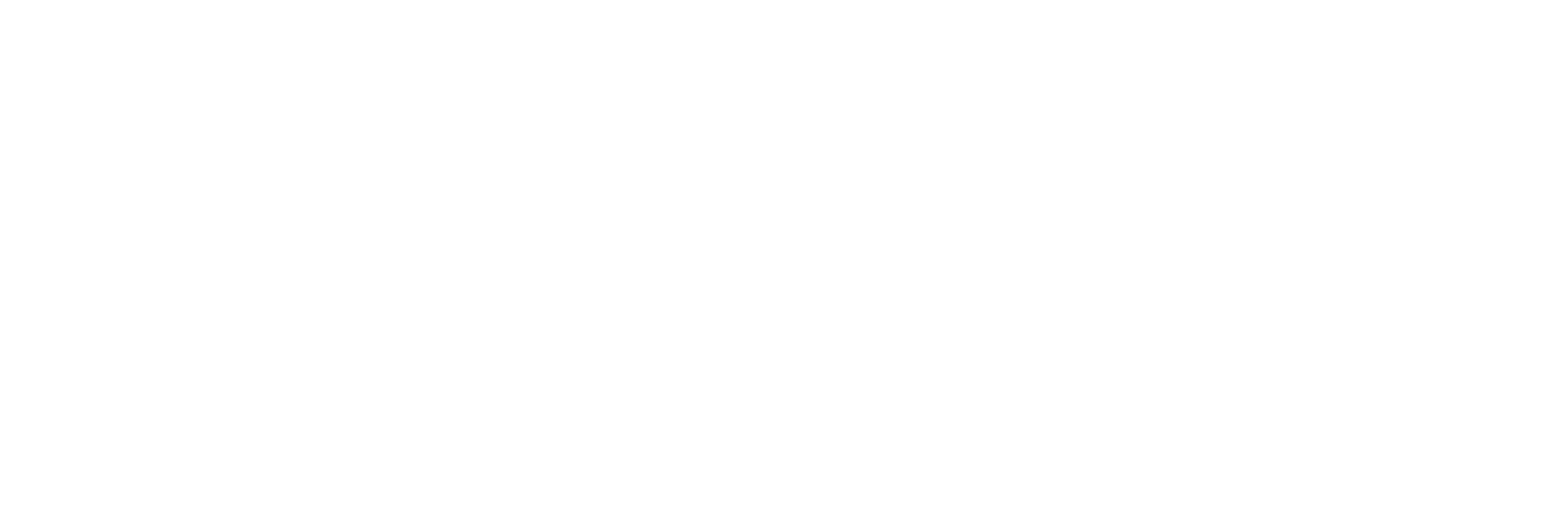
- Consultancy
- Online Courses
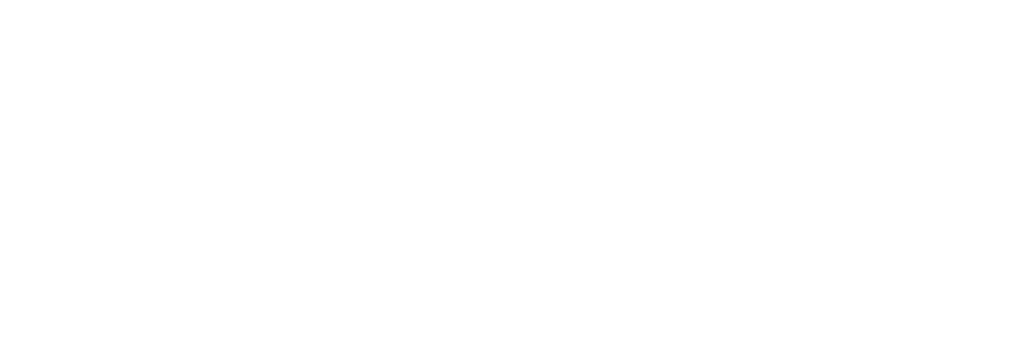
Join our Free Webinar
10th december 2024 | 1pm cet.

- Lean Business Model , Lean Six Sigma , Lean Wiki
DMAIC Model | The 5 Phase DMAIC Process to Problem-Solving
- 5 mins to read
- July 1, 2020
- By Reagan Pannell
Summary: An Introduction to DMAIC
Dmaic – the dmaic model.
The 6 Sigma DMAIC model remains the core roadmap for almost all Lean Six Sigma problem-solving approaches that drive quality improvement projects. It is used to ensure a robust problem-solving process is followed to give the best chance of the best solution being found.
A note about the structure and the approach used in this article.
Our approach to DMAIC follows Quentin Brook’s book “Lean Six Sigma & Minitab” which for anyone wishing to study Lean Six Sigma is a must for the Green Belt Course and the Black Belt Course .
What is the DMAIC Model?
DMAIC is short for: Define, Measure, Analyse, Improve and Control. These are the key phases that each project must go through to find the right solution. This flow is the concept behind DMAIC Analysis of an issue and its the DMAIC cycle all projects must go through.
As you can quickly see from the 5 DMAIC phases they follow a logical sequence as we will go through in more detail below. But they also make sure you do not try to jump to implementing a solution before you have properly, defined and measured what you are going to be an improvement.
We all love to jump to solutions, but the DMAIC problem-solving structure helps us have a more rigorous approach so that we do not short cut the process and perhaps miss the best solution or perhaps implement the wrong solution as well. It can help companies better structure their problem-solving approaches and be more robust in their approach.
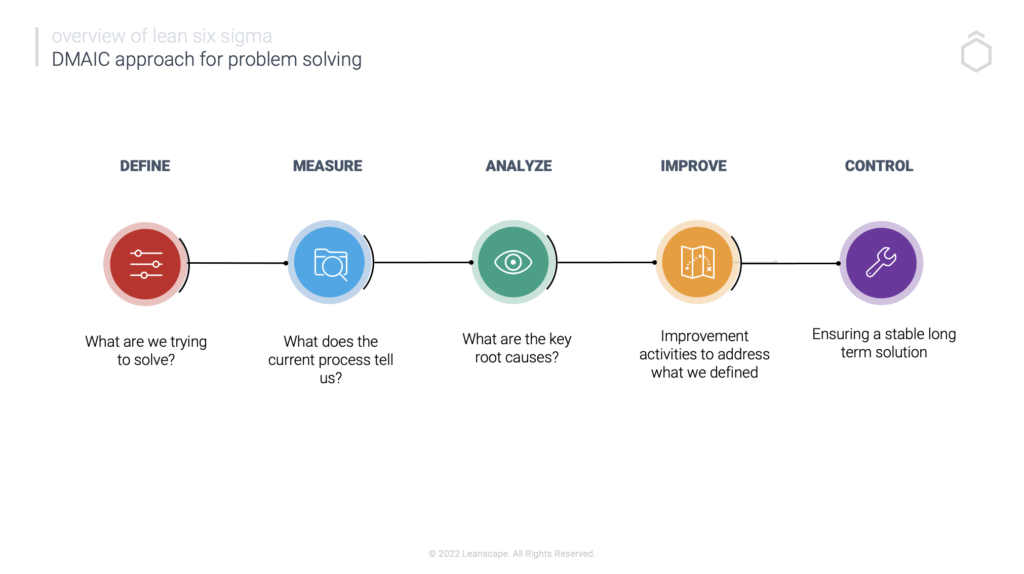
DMAIC – The 5 DMAIC Process Phases
The phases throughout the DMAIC model have and can be broken down in many different ways. One of the best approaches we have found is from Opex Resources which shows how to examine the existing processes, and with a project team, and the sigma improvement process, we can solve complex issues.
DMAIC Define Phase
The purpose of the Define phase is ultimately to describe the problems that need to be solved and for the key business decision-makers to be aligned on the goal of the project. Its about creating and agreeing the project charter .
All too often, teams have identified solutions without actually defining what it is they will actually be trying to do or perhaps not do. This can lead to internal confusion and often solutions which completely miss the business requirements and needs.
- Define the Business Case
- Understand the Consumer
- Define The Process
- Manage the Project
- Gain Project Approval
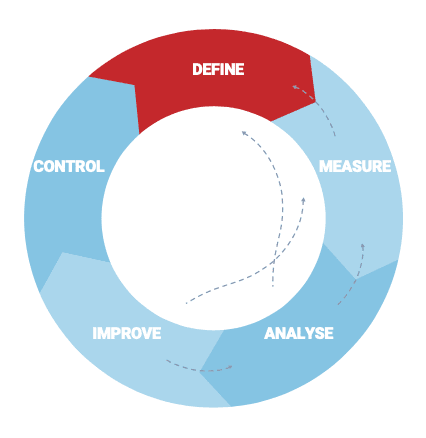
We can’t solve problems by using the same kind of thinking we used when we created them” Albert Einstein Tweet
DMAIC Analyse Phase
The goal of the DMAIC Analyse phase with the lean six sigma improvement process is to identify which process inputs or parameters have the most critical effect on the outputs. In other words, we want to identify the root cause(s) so that we know what critical elements we need to fix.
During this phase, the teams need to explore all potential root causes using both analytical approaches, statistical approaches or even graphical tools such as VSM’s and Process maps to uncover the most important elements which need to be changed/fixed.
The Analyse phase can be broken down into:
- Analyse the Process
- Develop Theories and Ideas
- Analyse the Data
- and finally, Verify Root Causes
DMAIC Improve Phase
The goal of the improvement phase is to identify a wide range of potential solutions before identifying the critical solutions which will give us the maximum return for our investment and directly fix the root cause we identified.
During this phase, the team brainstorm, pilot, test and validate potential improvement ideas before finally implementing the right solutions. With each pilot, the team can validate how well it improves the key measures they identified back in Define and Measure. When the team finally roll out the solution, the results should be seen if the right solution has been found and implemented correctly.
The Improve phase can be broken down into:
- Generate Potential Solutions
- Select the Best Solution
- Assess the Risks
- Pilot and Implement
DMAIC Control Phase
The final part of the DMAIC Model is the Control phase where we need to ensure that the new changes become business as normal and we do not revert to the same way of working as before.
During this phase, we want to ensure that we close the project off by validating the project savings and ensuring the new process is correctly documented. We also need to make sure that new measures and process KPI’s are in place and, finally that we get the business champion to sign off on both the project and the savings. We may need to redesign the workplace following the 5S principles .
The Control phase can be broken down into:
- Implement Ongoing Measurements
- Standardise Solutions
- Quantify the Improvement
- Close The Project
The key closing documents of the Control Phase is a Control Plan that documents all the changes and process steps with key risks, standard work instructions and the Project Close-Out document signed by the business owners to accept the change and the validated benefits.
Our approach to DMAIC follows Quentin Brook’s book “Lean Six Sigma & Minitab” which for anyone wishing to study Lean Six Sigma is a must for the Green Belt Course and the Black Belt Course .
The dmaic model vs. a3 management vs. 8d problem solving.
The DMAIC model is not the only project management roadmap. Two others which are important is the A3 format which originally comes from Toyota and is very Lean focused and the 8D which draws more of the DMAIC structure but with the 1-page idea of the A3.
Everyone has their own preference but each method is interchangeable. The DMAIC Structure lends its self naturally to a multi-slide Powerpoint presentation. Whereas the A3 is a single-page document which is perfect for internal communication and adding into War Rooms and Control Towers.
What’s important is that every problem-solving approach follows the PDCA (Plan, Do, Check and Act) Scientific Problem Solving format. The reset is just a preference or using the right tool in the right circumstances.
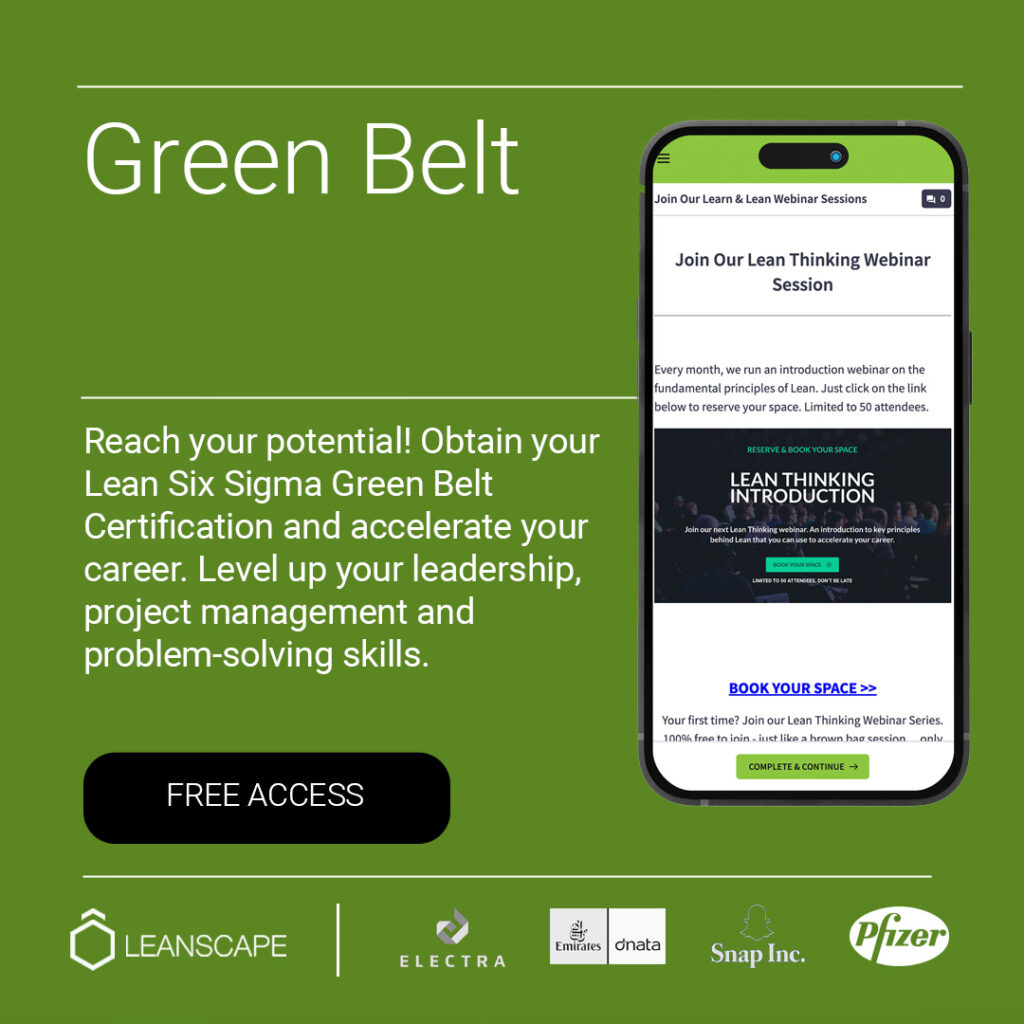
Accelerate success
Level-up today.
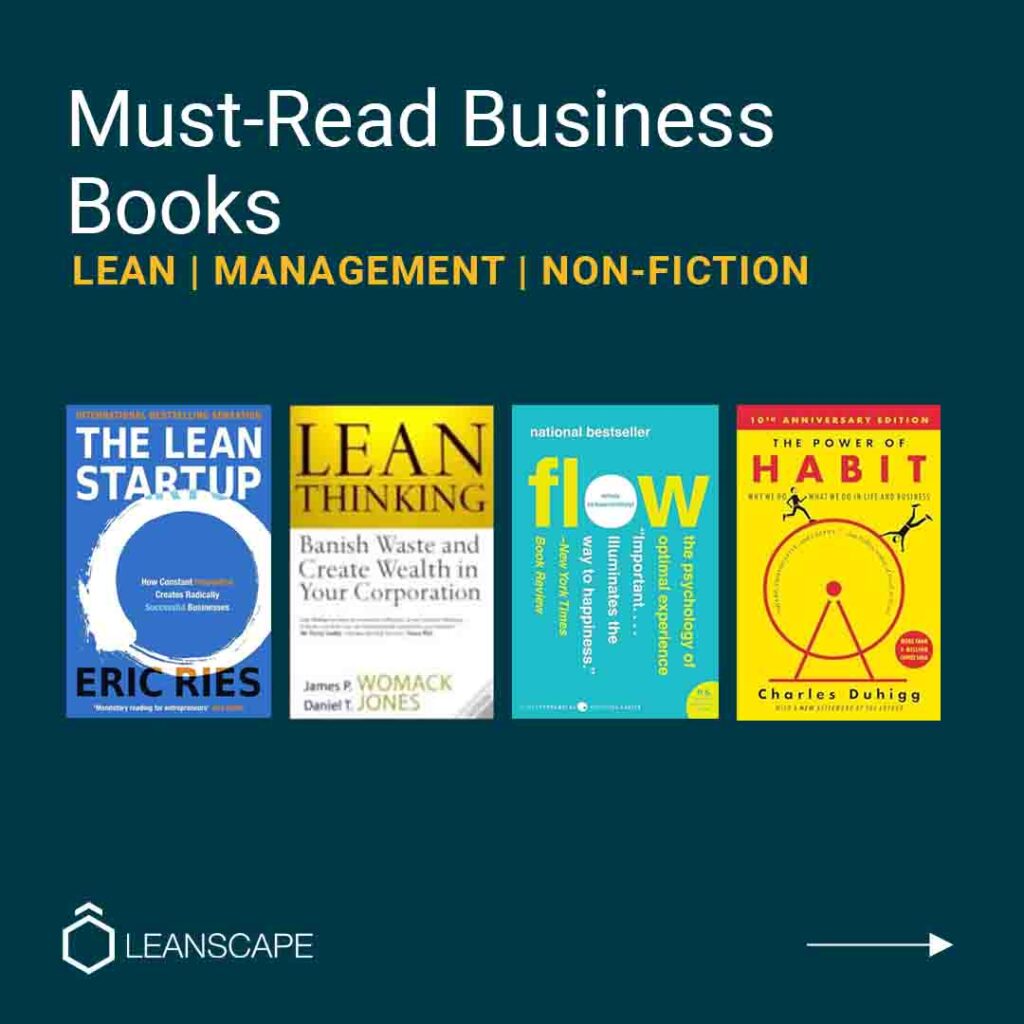
Similar Articles

Driving Enterprise Value: A Strategic Operational Transformation in the Events Industry

Visual Management in Digital Workspaces: Enhancing Operations
View all articles, other articles.
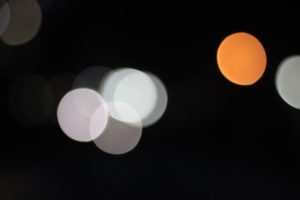
Harnessing the Power of the Leadership Circle Profile | Leadership
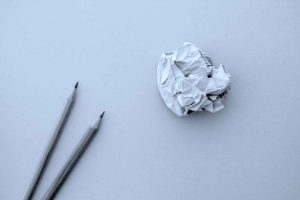
Unleash Your Business Growth Potential with a Deep Dive into the SCAMPER Brainstorming Technique
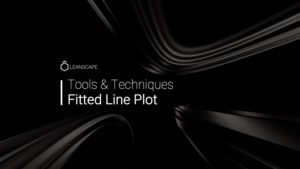
What is a Fitted Line Plot and how to create one in Minitab
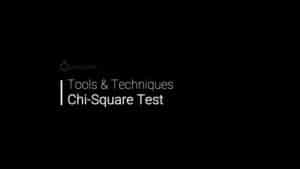
What is a Chi-Square Test and How Does it Work?
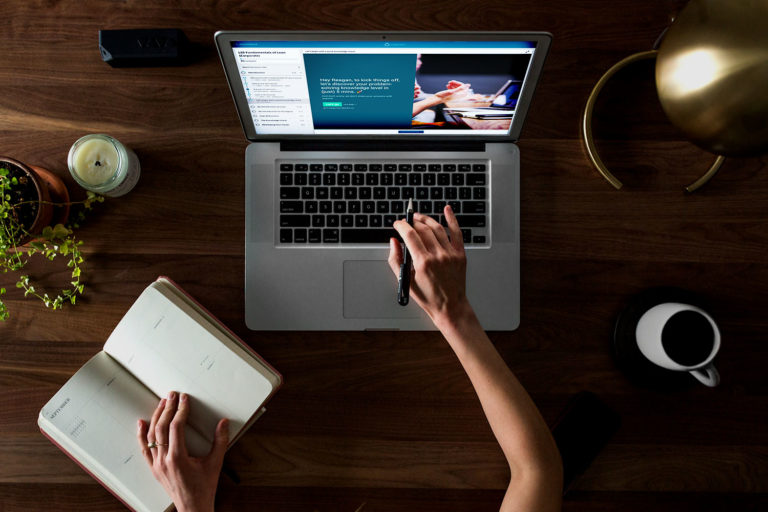
Online Business Courses Free: The Benefits for Professionals
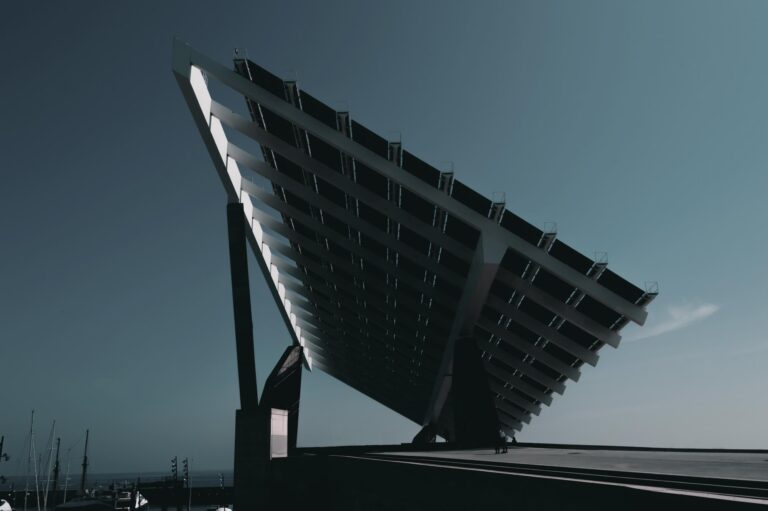
How to Optimize Energy Procurement Strategies for Your Business
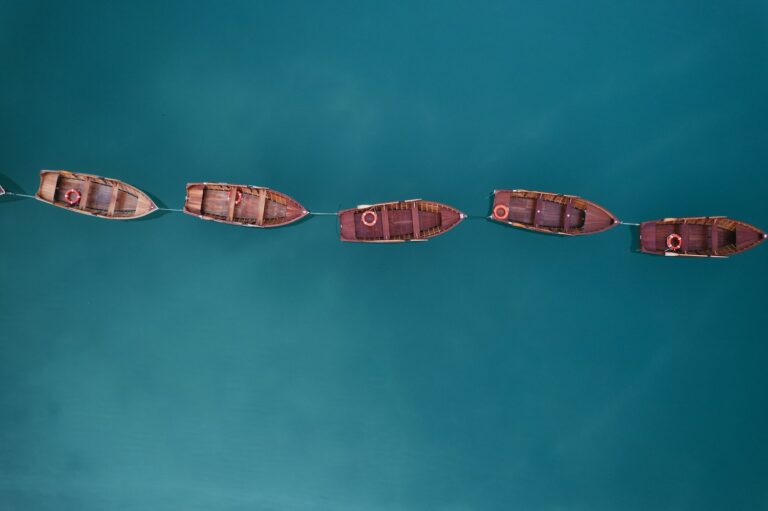
Realizing Results: Implementing Change with Precision
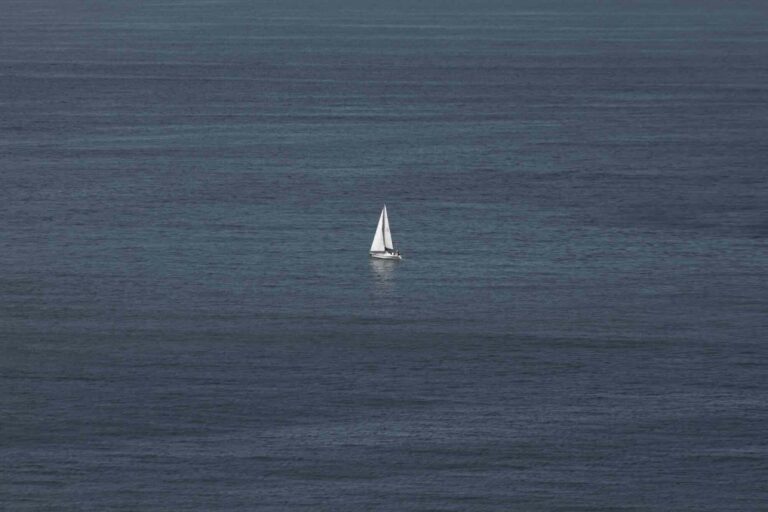
Mastering Enterprise Change: Strategies for Successful Transformation
Ready to talk i want to talk to your experts in business transformation so ..., related articles.
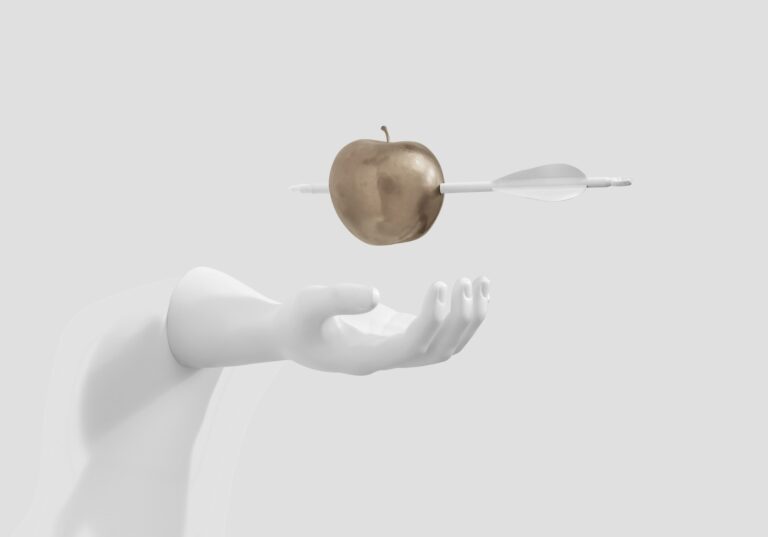
Visualizing Change: The First Step to Successful Transformation
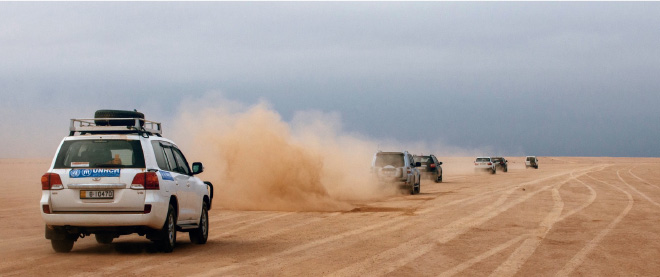
Fleet Management: Maximizing Fleet Efficiency for NGOs
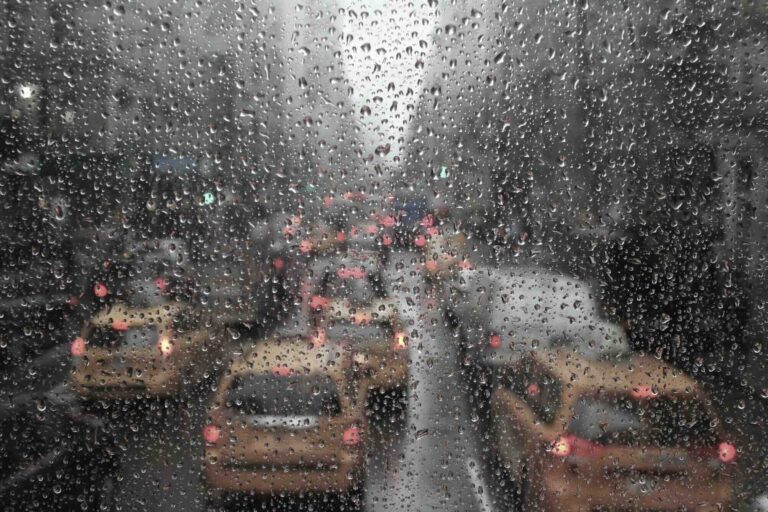
Mastering the Seven Wastes of Lean: Strategies for Effective Reduction
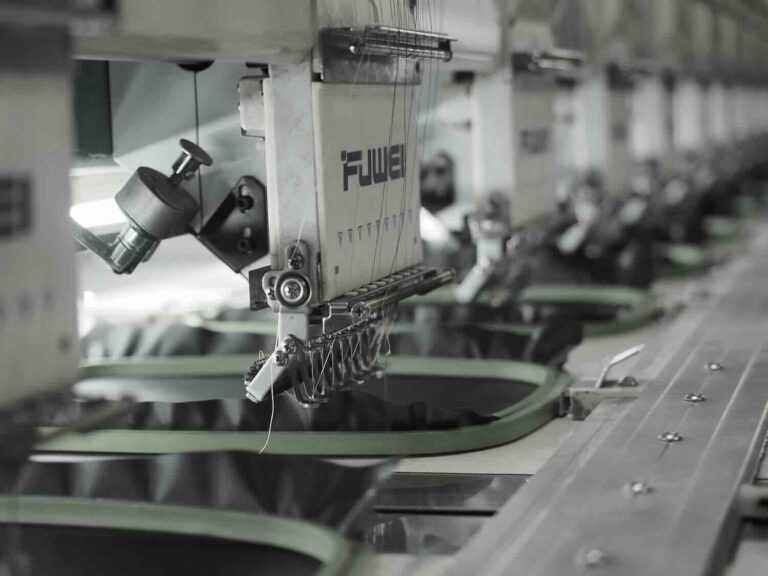
Mastering OEE Calculation Example: A Practical Approach to Efficiency
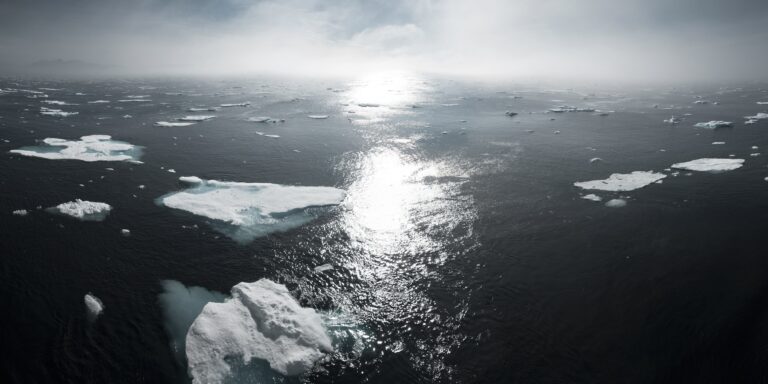
Why Leading Change Programs Often Fail to Deliver Real Change
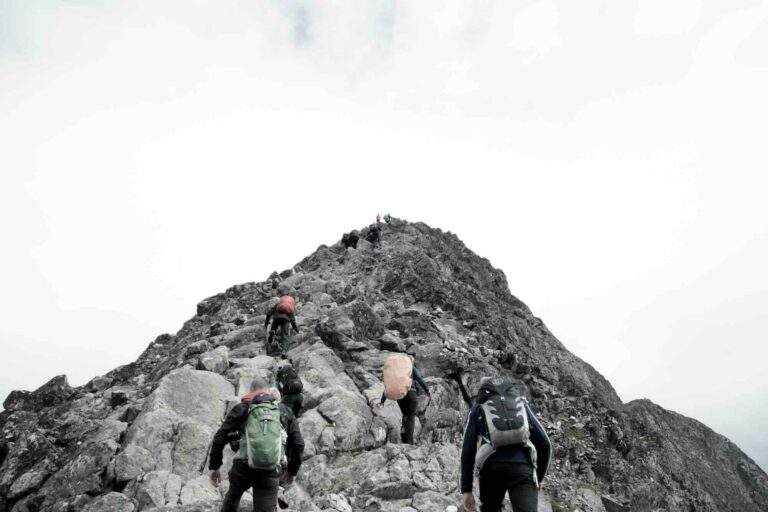
Leadership Skills Development Through Lean Thinking
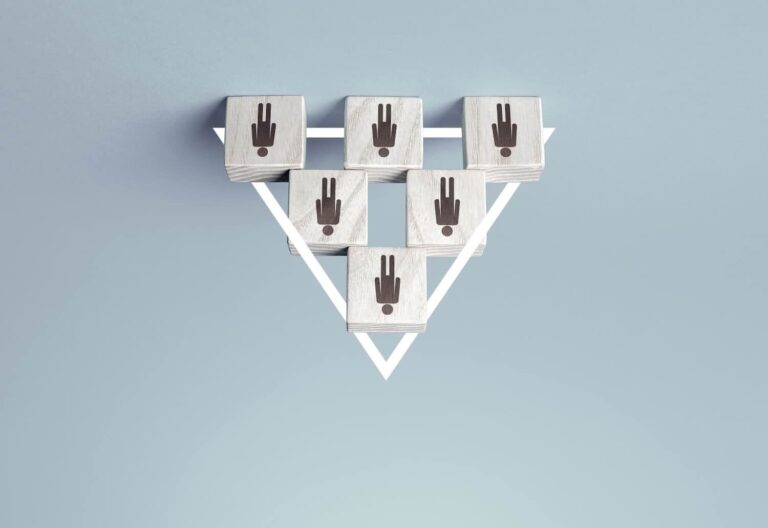
Mastering Operations Excellence: Strategies for Success and Growth
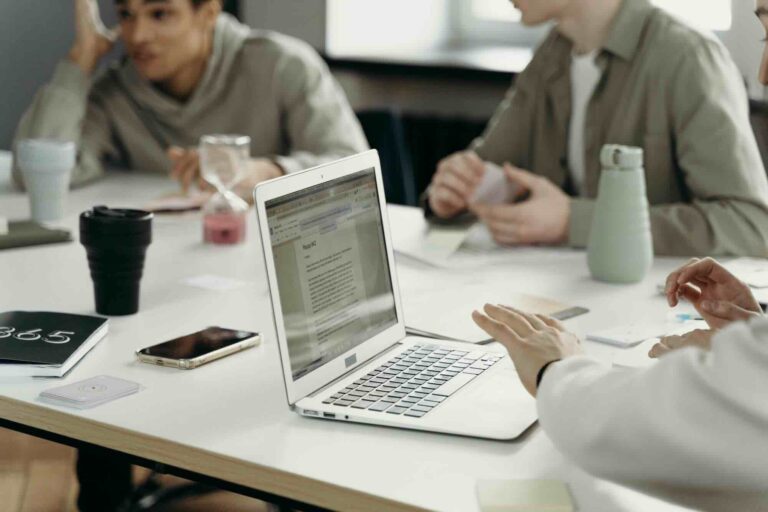
Using Lean to Improve Decision-Making Processes
Lean six sigma online courses.
FREE COURSE | YELLOW BELT | GREEN BELT | BLACK BELT | MASTERCLASS | WORKSHOPS
Fundamentals of Lean
Ready to start your journey into the world of Lean with this free course?
FREE COURSE
Lean Thinking
A Lean focused continious improvement certification course
LSS Yellow Belt
Propel your career forward, tackle complex problems and drive change
LSS Green Belt
The ultimate fast-track for future leadership
LSS Black Belt
Become an expert in change management and complex problem-solving.
TAKE OUR QUIZ
Which course is right for you.
Take our short quiz to find out which of our courses is right for you.
Join us for a Free Demo
We will talk you through our business transformation & lean training solutions, learn to lead the change.
- SALE ENDS IN:
— NEXT ONLINE WEBINAR STARTS 10th DECEMBER —
Join our webiner 25% off, take our business transformation quiz, are you ready for change.

IMAGES
COMMENTS
What Does DMAIC Stand For? DMAIC is an acronym that stands for Define, Measure, Analyze, Improve, and Control. It represents the five phases that make up the process: Define the problem, improvement activity, opportunity for improvement, the project goals, and customer (internal and external) requirements.
Jan 11, 2024 · DMAIC is the problem-solving approach that drives Lean Six Sigma. It’s a five-phase method—Define, Measure, Analyze, Improve and Control—for improving existing process problems with unknown causes. DMAIC is based on the Scientific Method and it’s pronounced “duh-may-ik.”
Nov 8, 2024 · DMAIC is an acronym for Define, Measure, Analyze, Improve, and Control. The DMAIC methodology is a systematic problem-solving methodology widely used in Lean Six Sigma projects to enhance processes and improvements. DMAIC tools help practitioners navigate each phase of this structured approach. Defining DMAIC Tools
Nov 29, 2022 · In this post, we will look at how to use the DMAIC process to solve problems. You will also find useful and editable templates that you can use right away when implementing DMAIC problem-solving in your organization. What are 5 the Steps of Six Sigma; DMAIC Process and Problem-Solving; Common Mistakes to Avoid when Using Six Sigma DMAIC Methodology
It uses statistical analysis and other tools to identify and eliminate the root causes of defects, and ultimately improve business performance. DMAIC, on the other hand, is the acronym that describes the five-step problem-solving process used in Six Sigma projects. It stands for Define, Measure, Analyze, Improve, and Control.
Jul 15, 2024 · Q: How does Six Sigma use DMAIC? A: DMAIC is a problem-solving approach that drives Lean Six Sigma. DMAIC’s five-phase method, Define, Measure, Analyze, Improve, and Control, improves existing process problems with unknown causes. Q: What are the DMAIC tools? A: DMAIC tools are, by phase: Define Phase: Project Charters, SIPOC Diagrams
Many improvement practitioners attempt to use the same DMAIC process, effective in solving the problem, as a framework for communication only to leave the audience confused and frustrated. One proposed solution to this problem is reorganizing the DMAIC information using the Minto Pyramid Principle's SCQA and MECE tools.
Aug 22, 2023 · The DMAIC Process is a data driven problem solving tool that can be used to improve, optimize and stabilize business processes. This cyclical problem solving model seeks to improve the processes performance within an organization. The acronym of this Lean Six Sigma tool stands for: Define, Measure, Analyse, Improve and Control. The base of this ...
Jul 1, 2020 · The 6 Sigma DMAIC model remains the core roadmap for almost all Lean Six Sigma problem-solving approaches that drive quality improvement projects. It is used to ensure a robust problem-solving process is followed to give the best chance of the best solution being found. A note about the structure and the approach used in this article.
Six Sigma tools are defined as the problem-solving tools used to support Six Sigma and other process improvement efforts. The Six Sigma expert uses qualitative and quantitative techniques to drive process improvement. Although the tools themselves are not unique, the way they are applied and integrated as part of a system is.